Precision Metal Stamping
Custom Component Part
We provide comprehensive metal stamping services, from initial design to final delivery, including material selection, process optimization, rapid prototyping, and large-scale production. Our expertise includes Progressive stamping and deep drawing stamping processes, ensuring customized solutions with high quality and efficiency to meet your specific needs.
Your One-Stop Solution for Advanced Metal Stamping Services
At Plantmetal, a division of Lingshantech, we specialize in designing and manufacturing complex progressive dies, heavy-duty deep drawing processes, and high-precision metal stamping services. Equipped with 20 presses ranging from 25 to 300 tons, featuring servo feed and die protection control, we are capable of mass production across a wide range of materials.
As a leading OEM manufacturer, we support high-volume metal stamping for industries such as automotive, electronics, and consumer goods, producing components like electronic connectors, contacts, clips, and more. Our continuous investment in equipment enables us to meet the evolving demands of various industries, improving production efficiency, competitive pricing, and product quality.
We offer comprehensive services, including metal stamping, mechanical engineering, prototype design, injection molding, and manufacturing support. Our collaborative product development approach ensures we work closely with clients to meet their specifications, preparing design-for-manufacturing (DFM) solutions and ensuring timely delivery.
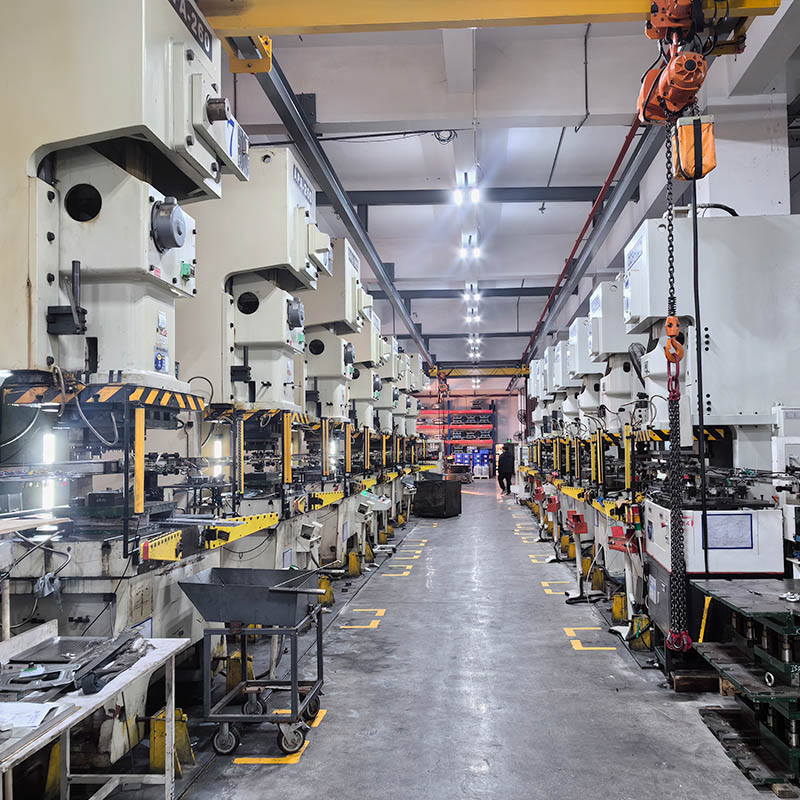
Featured Stamping Projects
WHAT WE OFFER
We are a trusted supplier specializing in the production of precision hardware components. Committed to consistently meeting your needs, we offer tailored solutions that align with industry-specific requirements. Our core services are designed to deliver superior performance, quality, and reliability.
Our facility features 25 punch presses, precision wire EDM machines, grinding equipment, welding and polishing tools, and ultrasonic cleaning systems. With advanced processing and testing capabilities, we deliver reliable, high-performance metal stamping solutions backed by stringent quality assurance.
- Custom Stamped Connectors
- Deep Drawing Sleeve
- Lead Frames
- Metal Clips
- Electronic Stamped Contacts
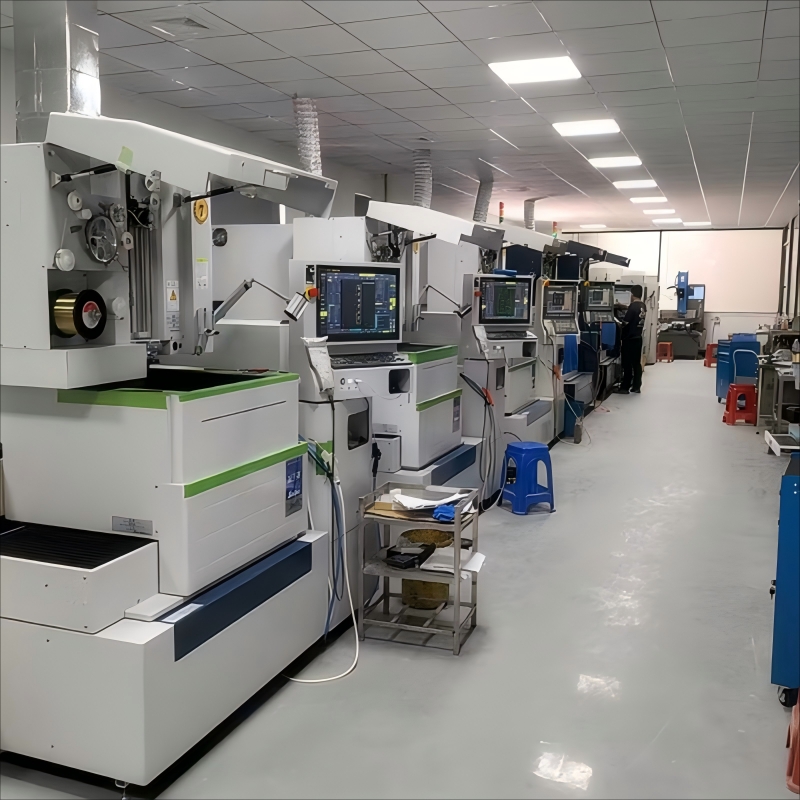
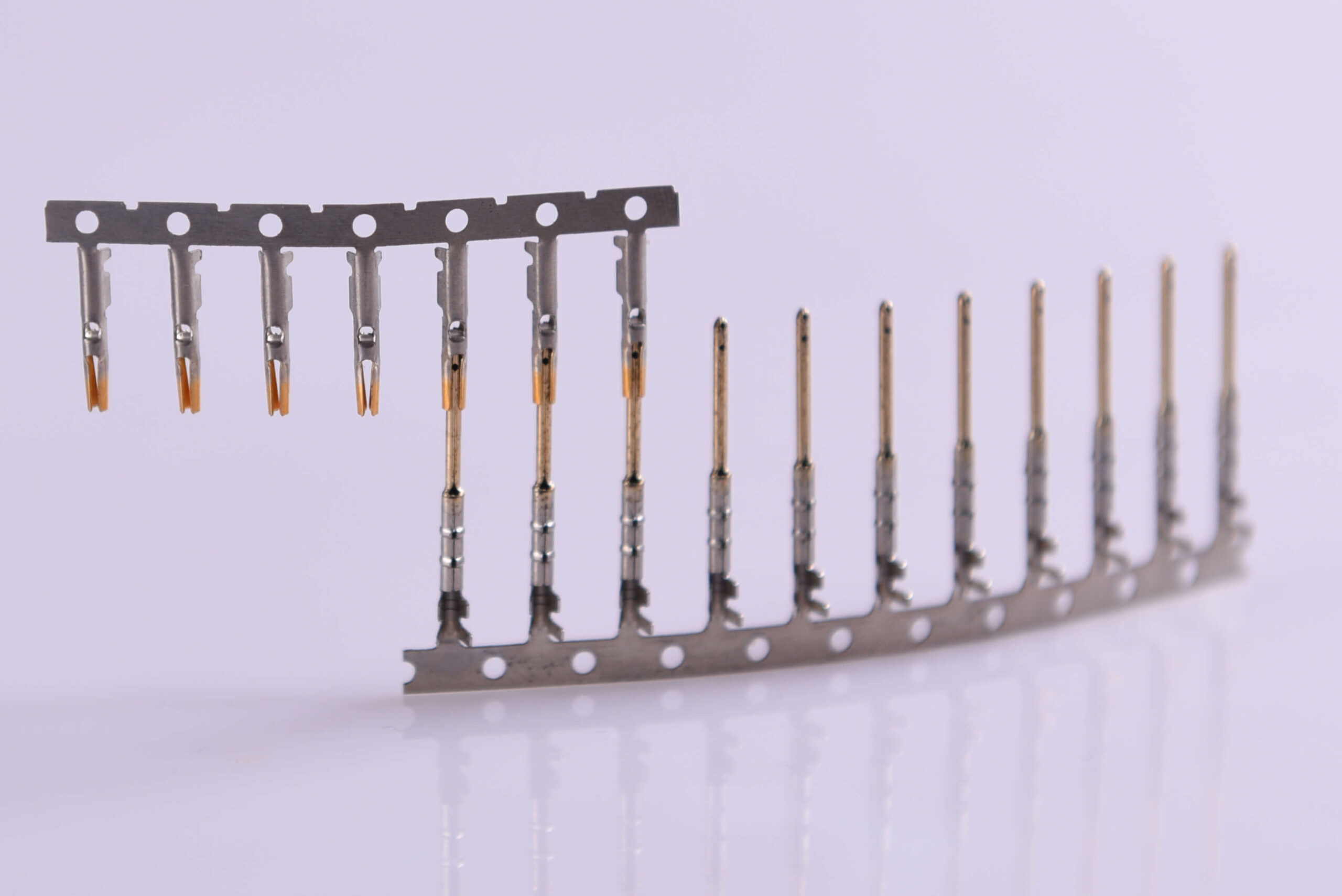
Custom Stamped Connectors
Material: Copper-5191
Post Process
Gold plating, silver plating, nickel-plating, tinplating
Applications of Custom stamped connectors
Aerospace Electronics: heavy duty aviation plug connector
New Energy: Heavy duty connector
Automotive: stamped connector
Deep Drawing Sleeve / Micro Deep Drawing Sensors Components
Material: Stainless steel 301/304, Aluminum-5052, Copper-1100,Copper-5191,Brass-6265,7275
Post Process
Stainless Steel: Passivation
Aluminum: Anodization
Copper: nickel plating, tinplating
Application Industry - Main industry sensor deep drawing parts
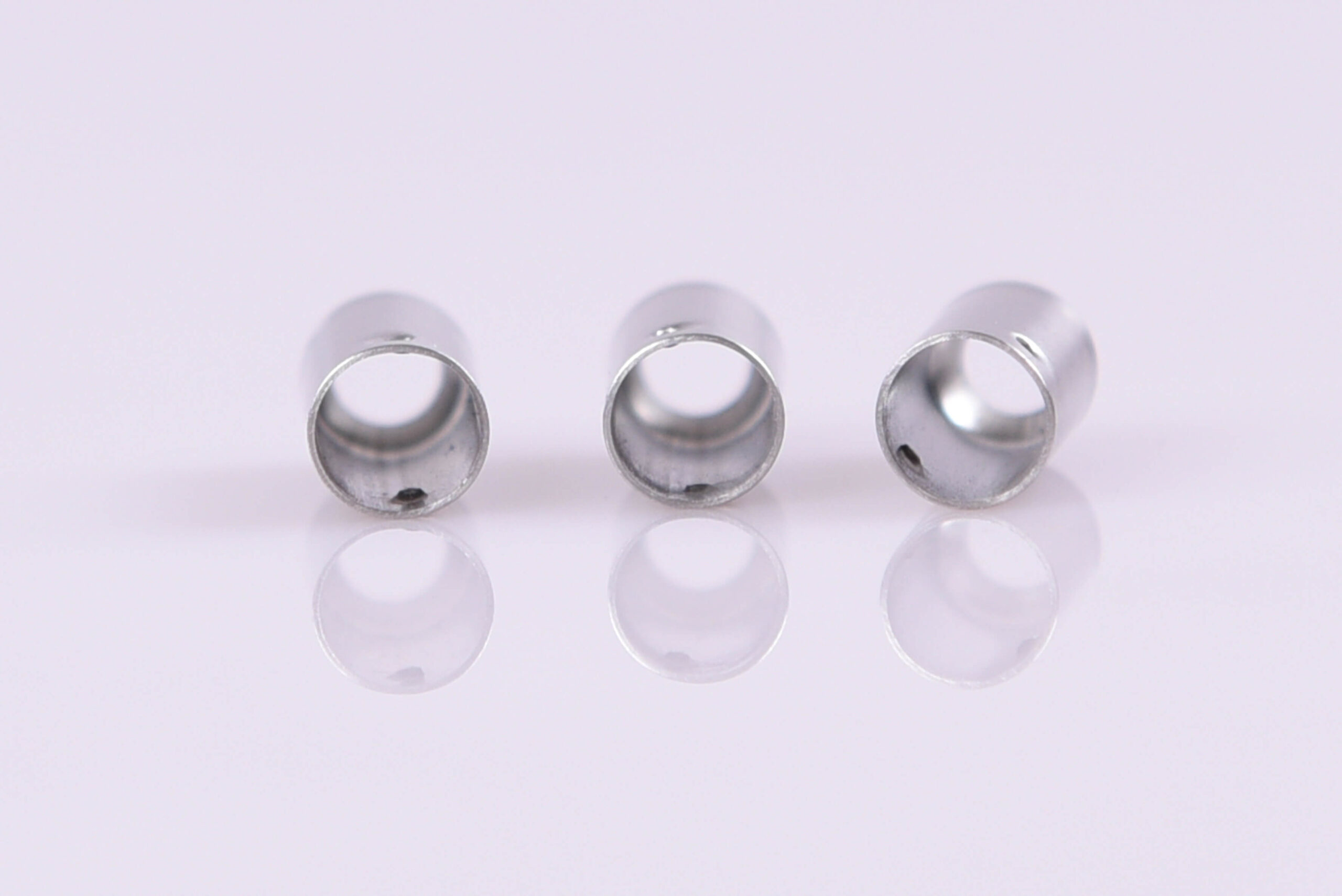
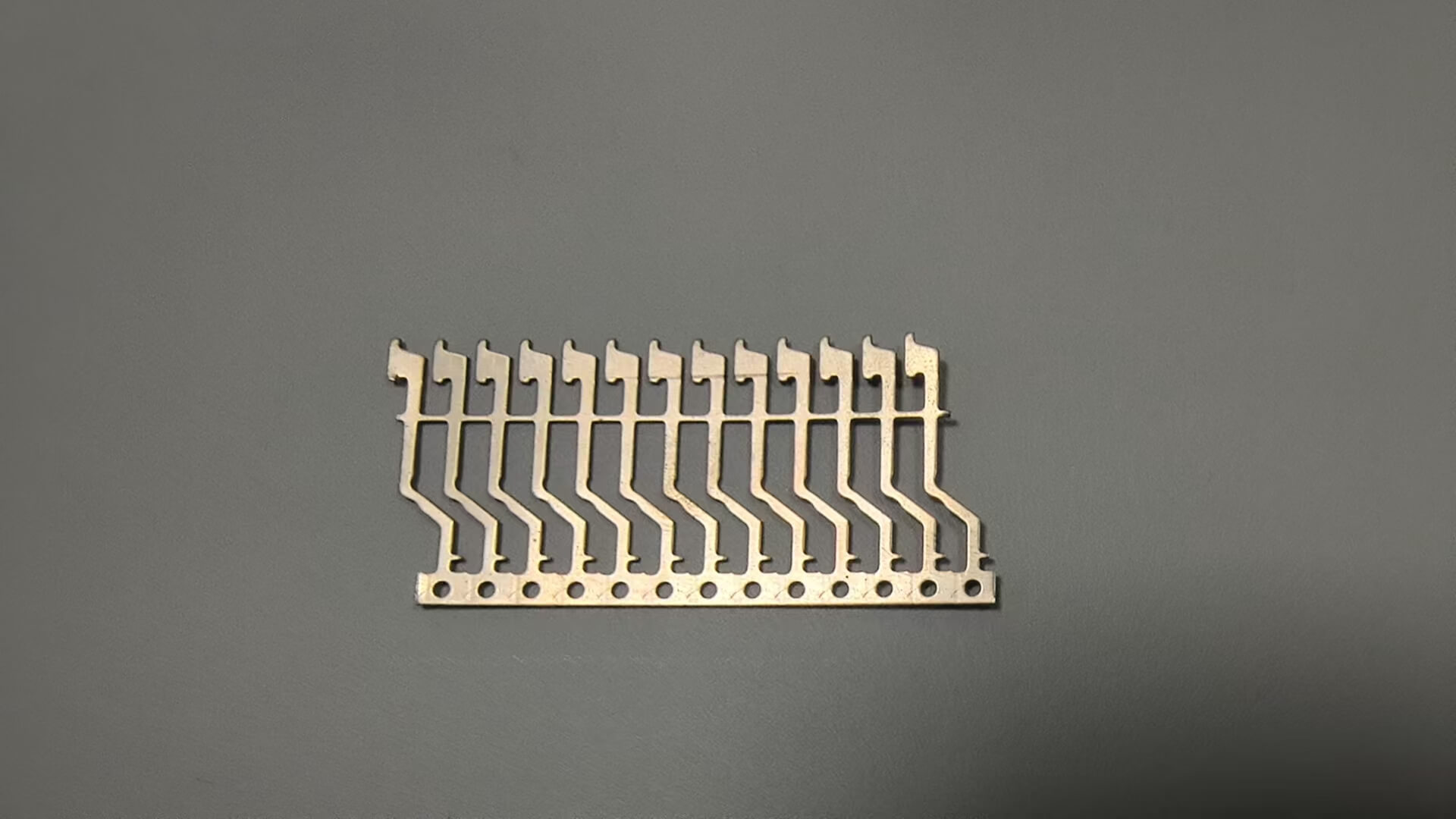
Lead Frames
Material: Copper-1100
Post Process
Copper: Passivation, Golden plating, silver plating, nickel plating, tinplating
Applications : Semiconductor and Electronics Industry,Automotive Electronics Industry,Telecommunications Industry,Consumer Electronics Industry,Industrial Control and Automation,Medical Equipment Industry
Car Air Control Button Shrapnel Metal Stamping Clips
Material: SUS301/631
Post Process
Copper: Passivation, Golden plating, silver plating, nickel plating, tinplating
Stainless Steel-Acid passivation, Temper to 250-280 ° C
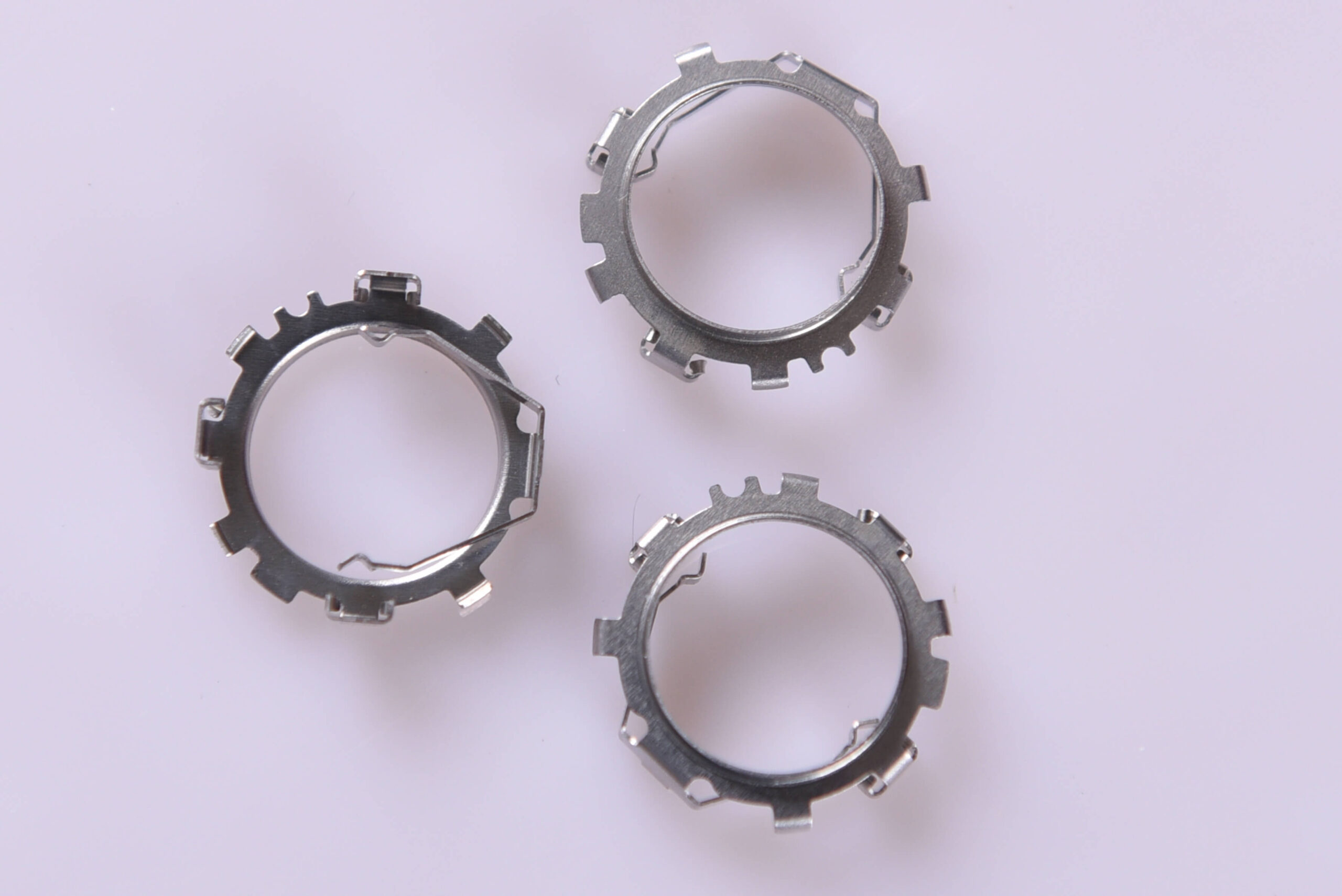

Terminal Connectors
Material: Copper-1100,Copper-5191,Brass-6265,7275
Post Process
Copper: Golden plating, silver plating, nickel plating, tinplating
Working With Plantmetal
Why Choose Us?
State-of-the-Art Equipment and Technology
Our investment in cutting-edge metal stamping equipment and technology includes high-speed presses, multi-station dies, and automated production lines. Utilizing these advanced tools enables us to achieve higher production speeds and greater efficiency in metal stamping operations.
Multi-Station Stamping Technology
We leverage multi-station stamping technology, allowing multiple processes such as cutting, bending, forming, and piercing to be executed simultaneously on a single press. This technology enhances production efficiency and reduces component handling and movement, leading to lower production costs.
Quality Assurance and Certification
Our commitment to delivering high-quality metal stampings is evidenced by our ISO 9001 and IATF 16949 certifications. We enforce rigorous quality control measures throughout the production process, including material inspection, process control, and finished product testing, ensuring each product meets stringent customer and industry standards.
High Precision and Consistency
We meticulously control process parameters and quality requirements at each production step to guarantee the precision and consistency of every metal stamping. Utilizing advanced measurement equipment and quality control tools, we ensure each product adheres to the specified requirements.
Material Selection and Optimization
We collaborate with suppliers to choose high-quality metal materials and optimize them based on customer specifications. This strategic material selection and optimization enhance the strength, corrosion resistance, and wear resistance of our products, meeting diverse application needs.
Engineering Support and Collaboration
Our experienced engineering team works closely with customers, providing technical support and solutions. We offer expertise in product design, process optimization, and cost control, helping customers achieve the best possible metal stamping solutions.