Core Processes for Deburring and Finishing Metal Parts
Deburring is a critical process that involves chamfering or rounding sharp edges on metal parts created during machining. This process is essential for removing burrs, sharp corners, and residual material left over from cutting tools or grinding operations. Effective deburring improves safety, functionality, and the overall quality of the metal parts.
Finishing processes are designed to refine the surface of a metal part, eliminating machining marks, scaling, or pitting. These processes not only enhance the aesthetic appeal of the part but also improve its functionality and prepare it for further treatments such as coating, plating, or painting. Finishing can include a range of techniques to achieve a smooth, polished, or textured surface, depending on the requirements of the final application.
Both deburring and finishing are crucial steps in the manufacturing process, and careful attention to these procedures ensures the production of high-quality, precision metal components.
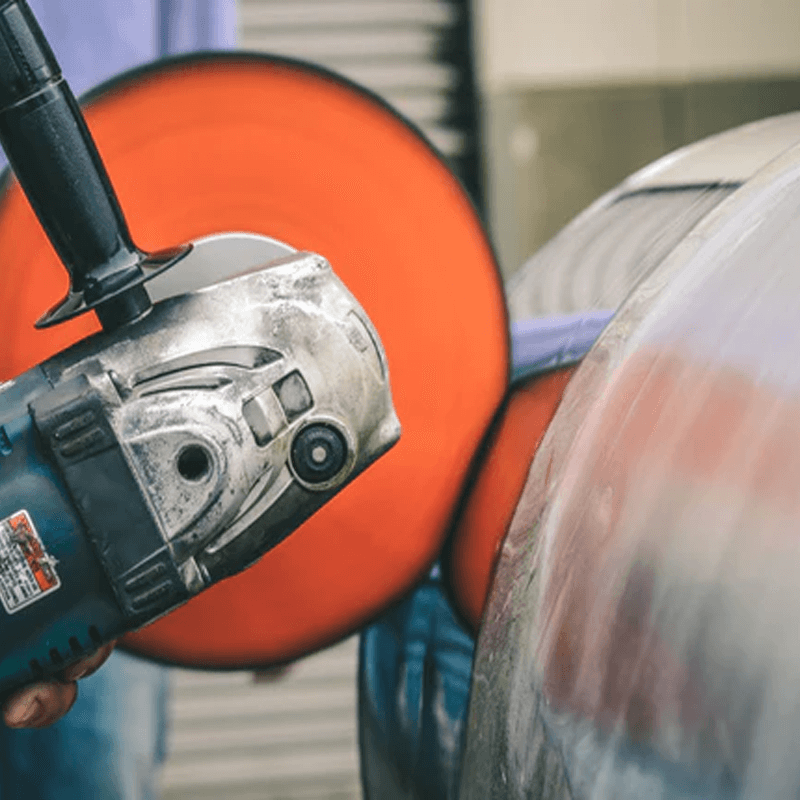
Hand Grinding, Sanding, Lapping, and Polishing
Despite advancements in manufacturing technology, manual processing remains an essential part of modern production. Many components, even those machined with advanced CNC equipment, are further refined through hand grinding, sanding, lapping, and polishing. Skilled machinists or toolmakers use a variety of tools—including files, stones, knives, abrasive sheets, compounds, and specialized deburring instruments—to achieve the desired finish as specified by engineering drawings. While these manual techniques are crucial for meeting precise specifications, they can be labor-intensive and costly. For large-scale production runs of identical parts, automated deburring and finishing processes are often employed to enhance efficiency and reduce overall costs.
Precision Ultra-Fine Cleaning Solutions
Our advanced cleaning technologies ensure that we meet the highest standards for part cleanliness. Utilizing both water-based and solvent-based methods, we provide comprehensive cleaning solutions tailored to specific client requirements. Our state-of-the-art equipment enables us to deliver meticulous cleaning results across various applications:
- In-Line Cleaning and Degreasing: Efficient processing of stamped and drawn parts directly on the production line.
- Bulk Cleaning Services: Thorough cleaning of large quantities of stamped and drawn components.
- Specialized Steel and Stainless Steel Cleaning: Expert cleaning for steel and stainless steel stamped parts to achieve superior cleanliness.
- Attenuation Analysis: Detailed assessment of particle reduction and contamination control.
- Particle Analysis: Comprehensive examination of both metallic and non-metallic particles.
- Particle Classification: Evaluation of particle types and sizes in accordance with VDA Volume 19 standards.
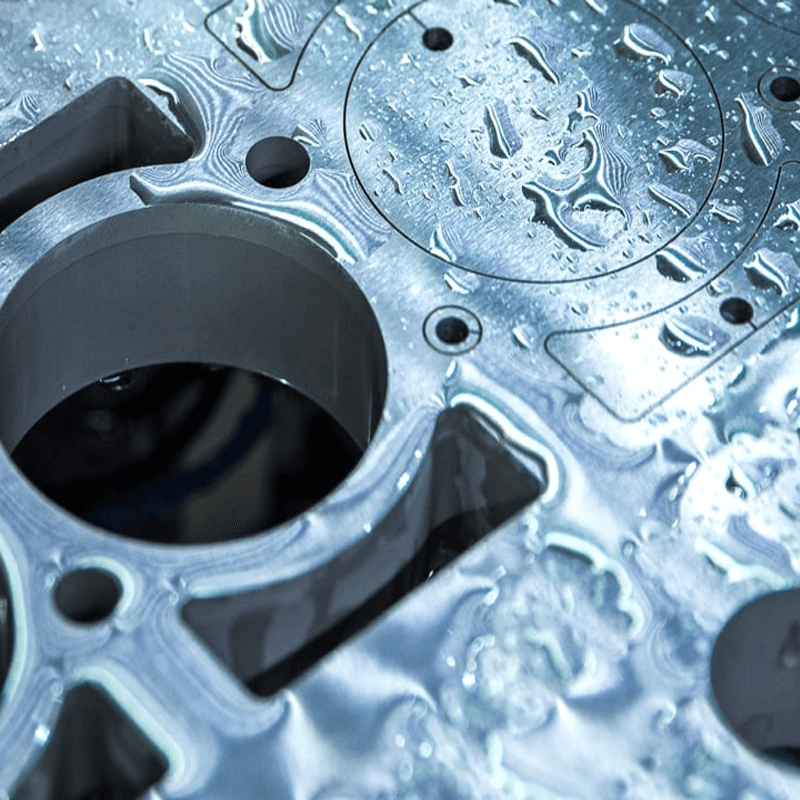
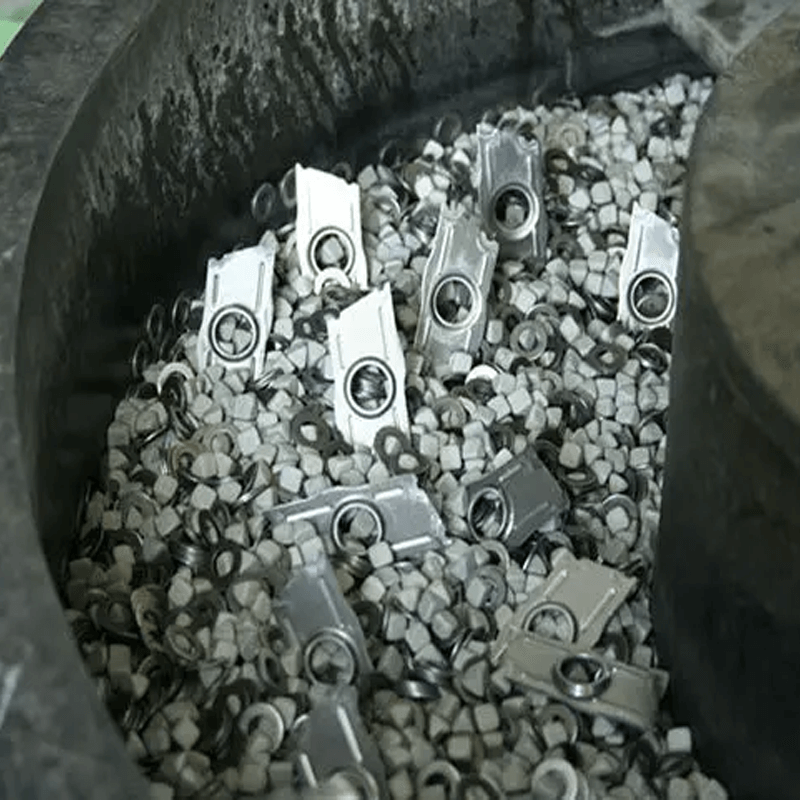
Mass Finishing
Mass finishing is a batch processing method that uses abrasive media and rotating or vibrating vessels to simultaneously deburr and finish multiple machined parts. This technique processes all surfaces in contact with the media. The equipment ranges from compact tabletop units ideal for jewelry and small components to large, rectangular machines designed for finishing substantial parts like aluminum aircraft components. The vessels are lined with durable rubber to safeguard both the equipment and the workpieces. A wide variety of media types and sizes are available, selected based on the physical attributes of the parts and the extent of material removal required to achieve the desired surface finish.
Powered Brush, Belt, and Disc Deburring and Finishing
Our advanced brushing systems are designed to efficiently remove burrs and surface imperfections from stamped strips, including stainless steel strips. This process often integrates cleaning and drying stages on the production line, ensuring compliance with strict particle cleanliness standards such as those specified in VDA Volume 19. Our equipment utilizes rotating abrasive discs, brushes, and drums, making it suitable for processing sheet or plate materials. Machines may create directional surface patterns or "grain," while robotic cells equipped with power tools and abrasives effectively address corners and finish intricate surfaces.
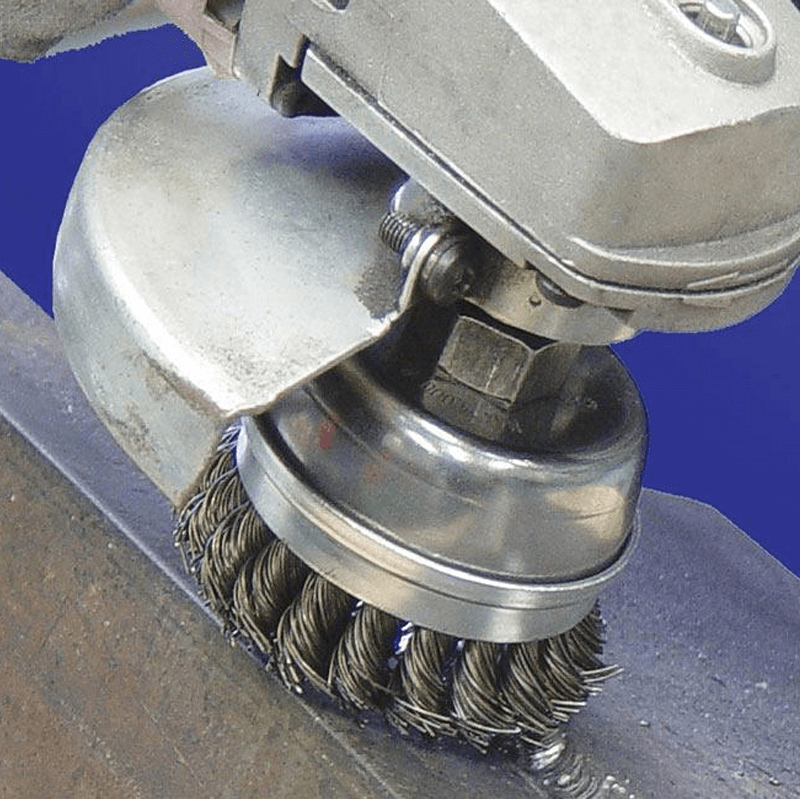
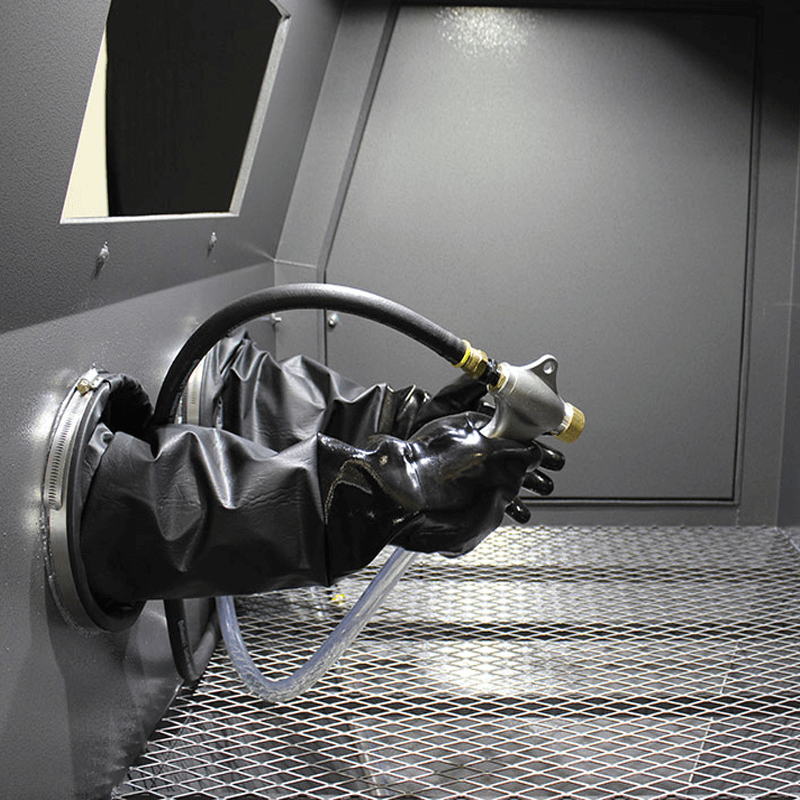
Abrasive Blasting
Abrasive blasting is employed to eliminate burrs and surface imperfections from individual parts using various blasting media. Glass beads and corundum are selected based on their effectiveness with complex geometries. This method accelerates solid abrasive particles, typically via compressed air, to impact the part's surface at high velocities. The choice of media—based on material hardness and desired surface finish—ensures that even the most demanding specifications are met. For smaller parts, enclosed cabinets are used to contain dust and protect operators, while robotic blasting systems and multi-nozzle machines automate the process for consistent results.
Electrochemical Deburring and Polishing
Electrochemical deburring and polishing utilizes anodic metal dissolution to refine a machined part's surface. This process involves a part-specific tool acting as the cathode, combined with an electrolyte fluid to create an anodic reaction. This controlled dissolution effectively removes surface material with high precision.
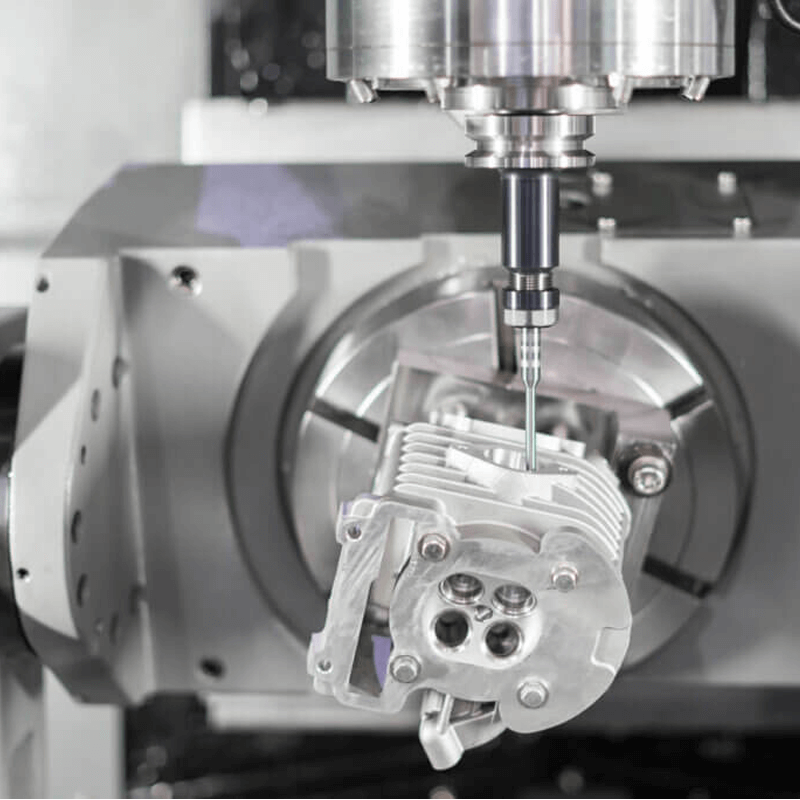
Thermal Aging
Thermal aging employs combustion gas ignition within a pressurized chamber to rapidly remove burrs from machined components. The process relies on the small size of the burrs, which ignite quickly in the oxygen-rich environment, vaporizing them. Residual oxide powder may need to be cleaned prior to subsequent coating processes. Accelerated thermal aging simulates product lifecycle conditions by exposing parts to rapid temperature fluctuations, ranging from -70°C to +180°C, to verify performance under extreme conditions.
Abrasive Flow Polishing and Deburring
The abrasive flow process uses reciprocating abrasive-laden slurry to polish and deburr surfaces and edges of complex parts. Two vertically opposed cylinders pump the slurry through passages created by the workpiece and specialized tooling. This method is particularly effective for deburring and polishing components with intricate internal features.
Plasma Surface Treatment
Plasma treatment involves using partially ionized gas with freely moving electrons to pretreat metallic surfaces before coating, printing, or bonding. The plasma effectively removes contaminants and activates the surface at a molecular level, significantly enhancing adhesion characteristics for subsequent processes.
Metal Surface Protection Processes
- Passivation: A process that cleans and conditions stainless steel to prevent corrosion.
- Cadmium Plating: Offers corrosion resistance, solderability, and antistatic properties, commonly used in aerospace applications. Available in clear, yellow, black, or olive drab finishes.
- Powder Coating: Provides exceptional durability and is an environmentally friendly alternative to traditional painting methods.
- Anodizing: Produces a uniform and durable oxide layer that is significantly harder than natural oxidation, and can be dyed for color finishes.
- Tin Plating: Used in the food industry and electronics for its solderability.
- Zinc Plating: Prevents oxidation and corrosion, extending the base material's lifespan.
- Chrome Plating: Primarily a decorative finish, chrome plating also reduces friction.
- Gold and Silver Plating: Ideal for ornamental purposes and used in electronics due to corrosion resistance.
- Black Oxide: Provides excellent indoor corrosion protection for products with oil or wax finishes.
- Annealing: A heat treatment process that softens material by decreasing its temper.
- Heat Treating/Aging: Increases material hardness and strength through controlled baking processes.