What Is Progressive stamping
Progressive stamping, also referred to as progressive die stamping, is a highly efficient metalworking process that involves feeding a continuous strip of metal through a series of dies, each designed to perform a specific operation. As the metal strip moves through these sequential dies, it undergoes various transformations until the final, fully-formed part is produced.
This automated process is capable of producing complex components with exceptional speed and precision, making it ideal for high-volume manufacturing. Progressive stamping is widely employed across industries such as automotive, aerospace, and electronics, where both precision and efficiency are critical to production demands.
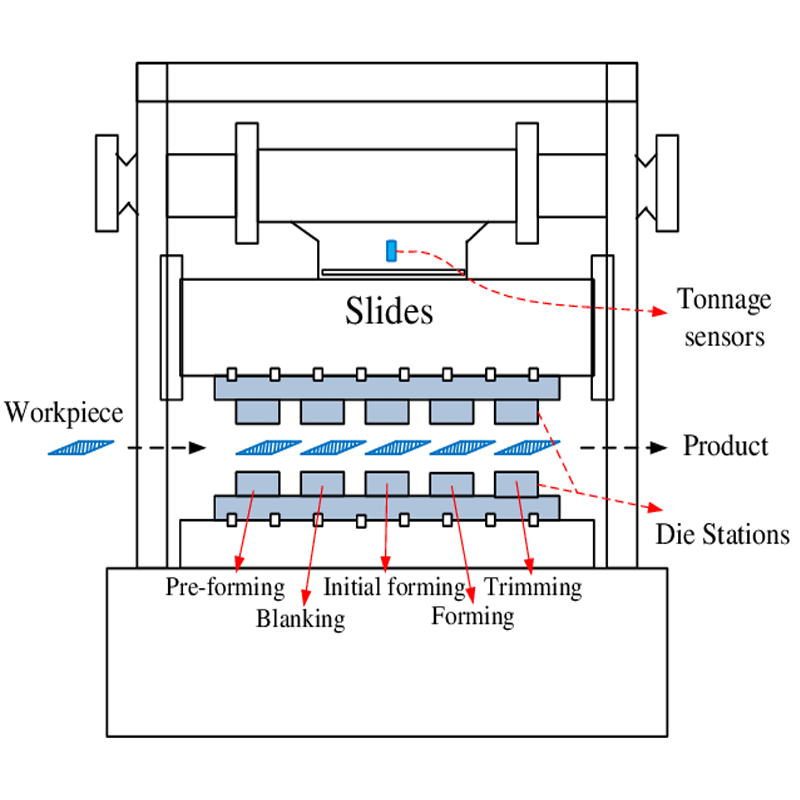
Advantages of Progressive Stamping
Progressive stamping provides several distinct advantages over traditional metalworking methods, including:
- High production efficiency: As a fully automated process, progressive stamping enables rapid production of large volumes of components with exceptional speed and efficiency.
- Cost-effectiveness: The integration of automated machinery and the ability to produce high quantities of parts reduce labor costs and make progressive stamping a highly economical solution for mass production.
- Precision and consistency: Each die in the progressive stamping process is meticulously engineered to ensure that every part is manufactured with a high degree of accuracy and uniformity, resulting in consistently superior quality.
- Material versatility: Progressive stamping is compatible with a wide range of materials, including steel, aluminum, copper, and other metals, making it adaptable to various industry requirements.
Why Choose Plantmetal for Your Progressive Stamping Needs
1. Advanced Machinery: Our facility is equipped with state-of-the-art progressive stamping machines that ensure precision, efficiency, and the ability to handle high-volume production runs with ease.
2. Expert Engineering Team: Backed by years of experience, our engineering team specializes in designing custom dies and optimizing the stamping process to meet even the most complex specifications.
3. Quality Assurance: We implement strict quality control measures at every stage of production, ensuring each part meets the highest industry standards for accuracy and consistency.
4. Cost-Effective Solutions: Our streamlined processes and automated technology reduce production costs, allowing us to offer competitive pricing without compromising quality.
5. Material Versatility: We have the capability to work with a wide range of metals, including steel, aluminum, copper, and specialty alloys, providing flexibility for various industry requirements.
6.One-Stop Custom Services: We offer comprehensive, end-to-end solutions, including custom die design, material selection, and finishing services, tailored to your specific requirements. Our one-stop approach streamlines the entire process, ensuring efficiency and precision from concept to completion.
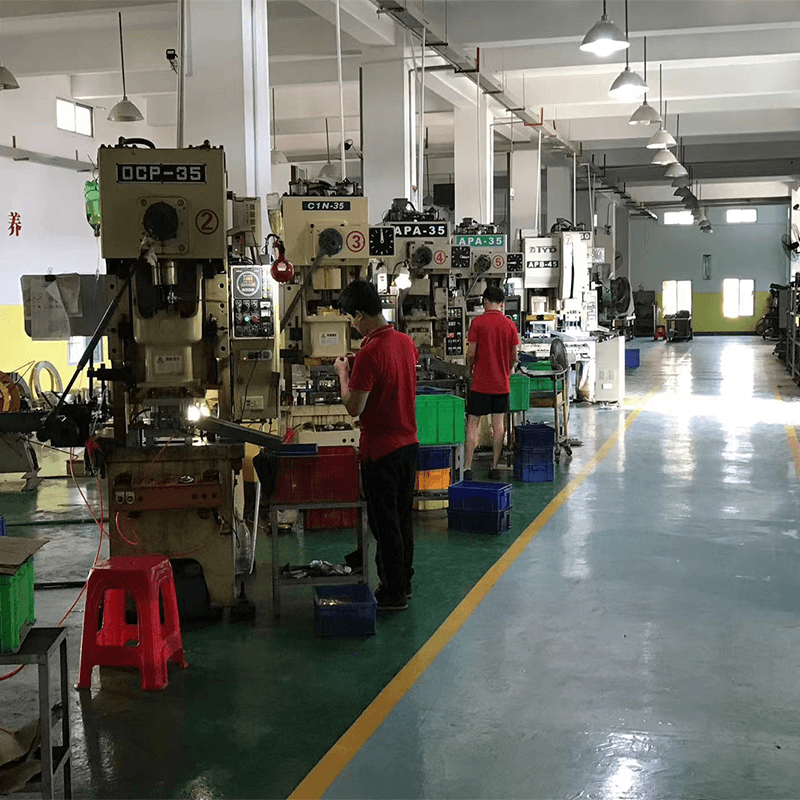
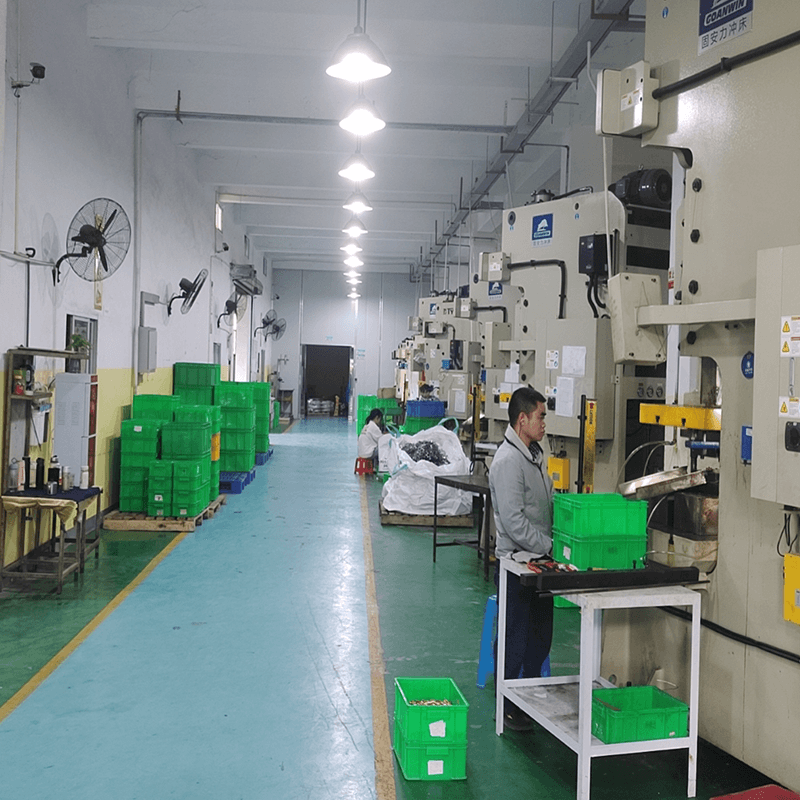
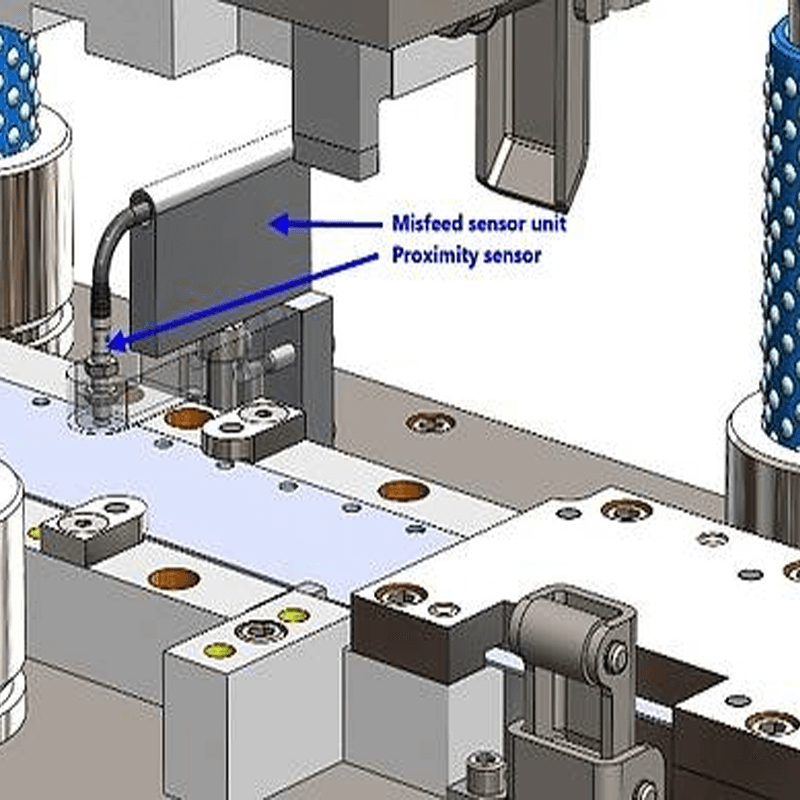
Machinery and Tools Utilized in Progressive Stamping
Progressive stamping relies on highly specialized equipment to carry out a range of operations on the metal strip. Key components of a progressive stamping system include:
- Feeder: The feeder's primary function is to guide and position the metal strip accurately into the machine for each stage of the stamping process. Depending on the machine configuration, the feeder can be either pneumatic or mechanical, ensuring precise alignment for each operation.
- Die Set: The die set consists of multiple dies, each dedicated to a specific task such as cutting, bending, or forming. This series of dies works in sequence to progressively shape the metal strip into the desired part.
- Press: The press is the core of the progressive stamping machine, providing the necessary force to carry out each operation. Depending on the application, presses can be mechanical or hydraulic, offering the power and precision needed for efficient production.
- Stripper: The stripper plays a crucial role in removing the finished part from the metal strip after each operation, ensuring the part is released smoothly and without causing any damage to the component.
- Additional Components: Progressive stamping systems may also incorporate advanced features such as sensors for real-time monitoring, lubrication systems to reduce friction, and safety mechanisms to ensure smooth and secure operations throughout the process. These elements enhance efficiency and overall production quality.
The Progressive Stamping Process
Step 1: Design and Engineering
The progressive stamping process begins with the design and engineering phase. This critical step involves developing a detailed design for the part, while determining the most efficient and effective method to manufacture it using progressive stamping. Prototypes may be produced during this phase to validate the design and allow for any necessary refinements before moving forward.
Step 2: Tooling Development
Once the design is finalized, the next step is to develop the tooling. This involves creating precision-engineered dies that will perform the various stages of metalworking on the strip. The dies are typically crafted from high-grade hardened steel to endure the substantial forces and pressures of the stamping process, ensuring durability and consistent performance.
Step 3: Machine Setup
After the tooling is complete, it is installed into the progressive stamping press. The machine is meticulously configured to ensure the metal strip is properly fed through the dies and that each operation is executed with high precision. Fine-tuning the setup is essential to guarantee that every stage of the process runs smoothly.
Step 4: Full-Scale Production
With the setup finalized, the production phase begins. The metal strip is continuously fed through the progressive stamping machine, with each die performing its designated operation. The process results in the finished part, which is then separated from the strip and subjected to rigorous quality inspections to ensure it meets all specifications and standards.
Materials Used in Progressive Stamping
Progressive stamping accommodates a wide range of materials, including steel, aluminum, and copper, each selected based on their unique properties and the specific requirements of the part being produced. These materials are favored in progressive stamping for their ability to endure the high pressures involved in the process while maintaining their structural integrity. The choice of metal largely depends on the desired characteristics of the finished product and the application for which it is intended.
Steel
Steel is a highly versatile material that can be efficiently formed and shaped during progressive stamping, making it suitable for producing parts with complex geometries and intricate features. Its excellent strength-to-weight ratio and durability make it ideal for applications requiring robust, long-lasting components. Steel's high tensile strength allows it to withstand the forces of progressive stamping without deforming, ensuring the precision of tight tolerances and structural integrity. Additionally, steel is widely available and cost-effective, offering a balance between performance and affordability. Its adaptability allows manufacturers to create a broad range of parts for various industries, from automotive to industrial applications.
Aluminum
Aluminum is known for its excellent formability, making it well-suited for parts with intricate designs and complex geometries. It can be bent, shaped, and formed easily without compromising its structural integrity. This characteristic is especially valuable in industries such as aerospace and automotive, where weight reduction is critical. Aluminum’s low density makes it significantly lighter than steel, offering an optimal solution for applications requiring high strength but low weight. Furthermore, aluminum exhibits excellent electrical conductivity, making it a preferred material for electrical and electronic components. Its high thermal conductivity also makes it an ideal choice for parts designed for heat dissipation, such as heat sinks and cooling systems. Progressive stamping enhances aluminum's ability to form detailed, precise components efficiently and cost-effectively.
Copper and Copper Alloys
Copper and its alloys are excellent choices for progressive stamping when electrical conductivity is a primary concern. Renowned for their superior conductivity, copper materials are frequently used in the electrical and electronics sectors. The progressive stamping process allows for the precise creation of intricate designs in copper parts, enhancing their ability to conduct electricity and ensuring effective connectivity. Copper alloys, which blend copper with other metals, offer additional advantages such as increased strength, improved corrosion resistance, and other enhanced properties while retaining good electrical conductivity. These attributes make copper alloys a reliable option for applications requiring both durability and performance.
Exotic Metals
Exotic metals, a broad category that includes high-strength alloys like titanium, magnesium, and specialty steels, are often used in progressive stamping when parts require unique performance characteristics that cannot be achieved with more common materials. These metals are designed to offer specific properties such as extreme durability, lightweight strength, or enhanced resistance to environmental factors. Industries like aerospace, medical devices, and high-tech electronics frequently use exotic metals for their demanding applications. Progressive stamping provides the precision and adaptability needed to shape these materials into complex, high-performance components, ensuring their suitability for specialized and highly demanding environments.
Applications
1. Automotive: Producing components like brackets and electrical connectors for vehicle manufacturing.
2. Aerospace: Creating lightweight structural parts and fasteners to meet safety standards.
3. Electronics: Manufacturing intricate components such as connectors and circuit boards.
4. Medical Devices: Fabricating high-precision parts for surgical instruments and medical device housings.
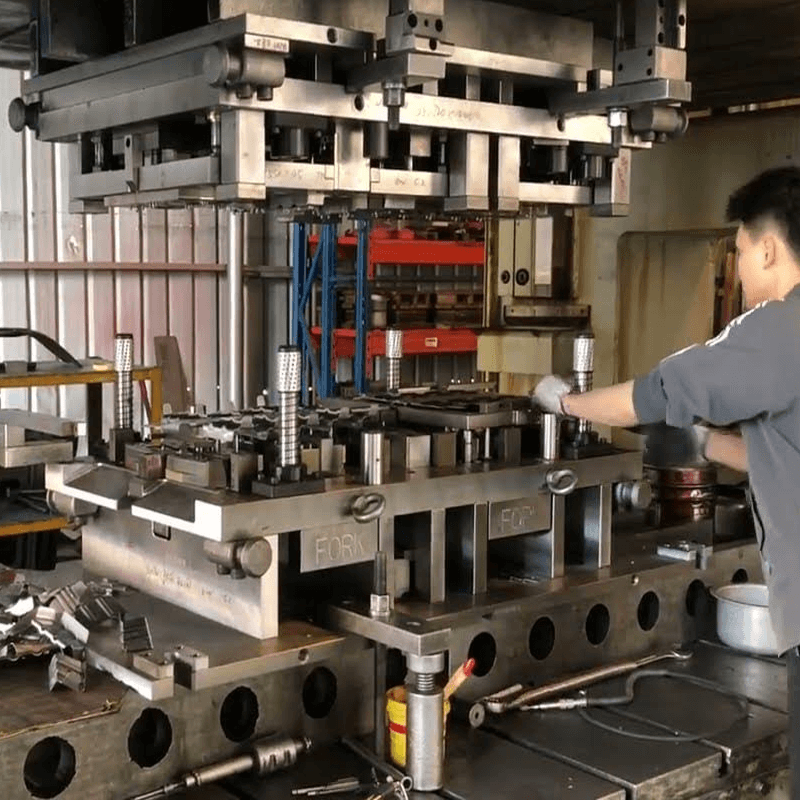