About Plantmetal
Founded in 1998 in Xiamen, China, Plantmetal is a leading manufacturer specializing in precision metal components. We excel in designing and developing metal molds, as well as fabricating a diverse range of metal parts, including OEM stamping components, CNC machined parts, silver contacts, clips, and automotive components.
Over the past two decades, we have built a strong reputation for delivering high-quality metal parts tailored to our clients' custom projects. Our dedication to excellence and customer satisfaction has earned us the prestigious ISO13485 and IATF16949 certifications.
At Plantmetal, we are committed to offering outstanding customer service throughout the entire process, from the initial consultation to the final delivery of your order.
- Metal Stamping
- Slide Forming
- Automated Assembly
- Wire Forming
- Welding
- Tooling
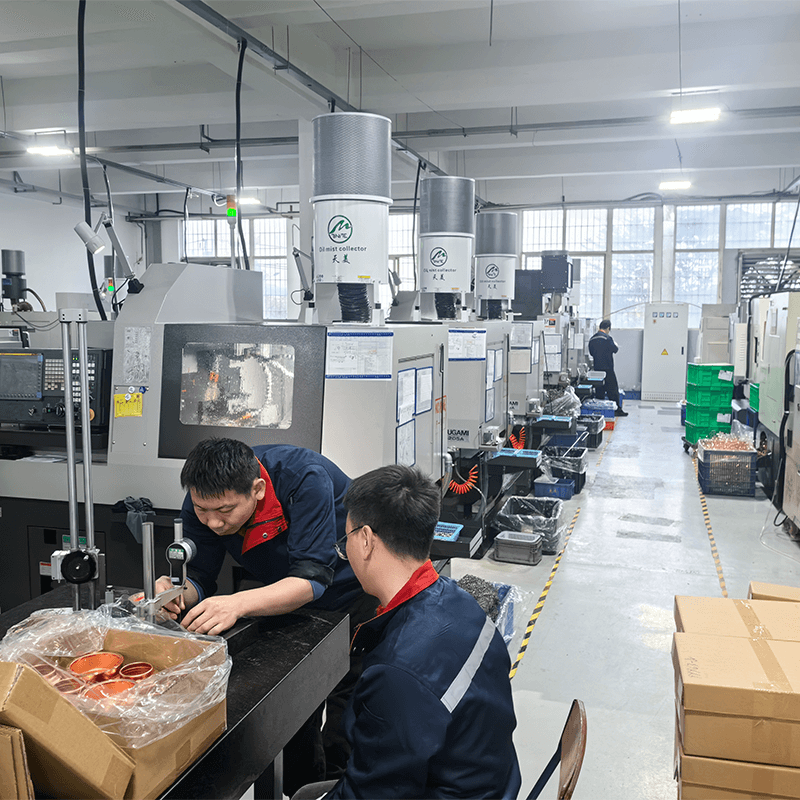
Commitment to Product Engineering Ensures Superior Quality
At our company, we view our work as more than just metal forming; we see it as crafting solutions and addressing challenges for our clients through practical and cost-effective manufacturing methods. Our focus on product engineering allows us to deliver exceptional quality and innovative solutions tailored to meet our customers' specific needs.
Our Team
With each team member bringing over 20 years of experience in metal parts manufacturing, we pride ourselves on our exceptional expertise and high level of customer satisfaction, consistently achieving ratings above 95%. Over the past two decades, our skilled professionals have delivered tailored solutions to more than 300 clients, successfully reducing project costs by an average of 30%.
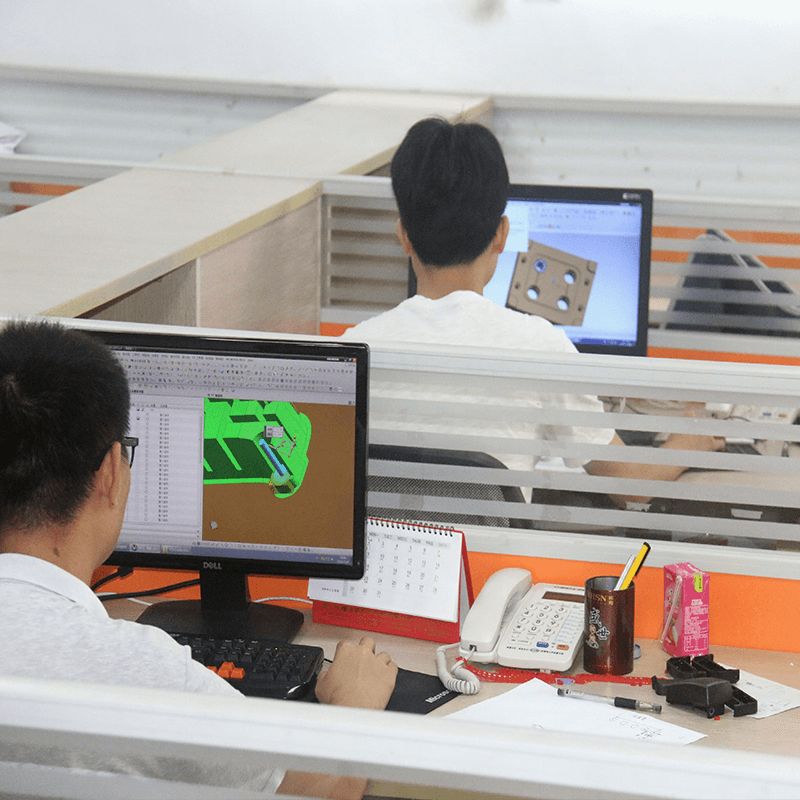
Metal Stamping Capabilities
Metal stamping is a cornerstone of our manufacturing expertise. Our facility is equipped with an array of precision presses, ranging from 45T to 2000T, capable of producing complex automotive structural components. At Plantmetal, we offer a full spectrum of stamping services to meet diverse production needs.
- Suitable for low-volume production
- Certified to ISO 13485 and IATF 16949 standards
- Achievable tolerances: +/- 0.01mm
- Surface roughness: Ra 0.8μm
Tooling Design & Mold Manufacturing
Our in-house tooling design and mold manufacturing capabilities are integral to supporting our stamping operations. We offer a fully integrated production line that encompasses every stage of mold creation—from design and development to testing and mass production. This process is engineered for efficiency and precision, guaranteeing on-time delivery and cost-effective solutions.
- Expertise in progressive and single die tooling
- Mold material: SKD11
- Mold lifespan: up to 500,000 cycles
In-Die Welding & Riveting at Plantmetal
Plantmetal has recently launched an advanced in-die welding and riveting production line, specifically tailored for the assembly of electronic contacts. This cutting-edge line has boosted our production capacity by a factor of 50 compared to traditional multi-component assembly methods.
- Tolerance: +/- 0.01mm
- Ideal for high-volume production
- Designed to maximize the profitability of our clients' products
Customized OEM Manufacturing Solutions
Small Batch Production
We accommodate low minimum order quantities (MOQ) and accept small-scale orders. Depending on your project needs, we offer a variety of options, including CNC machining and lathe milling compound processing.
- Production Capacity: 100-1,000 units
- Lead Time: 16 business days
High-Volume Manufacturing
Our high-speed punch presses are designed to meet large-scale production requirements. From mold creation to production and final delivery, we ensure superior quality while minimizing lead times.
- Production Capacity: 1,000+ units
- Lead Time: 25 business days
Custom Fabrication Services
We specialize in producing single-piece, small-batch, and complex custom parts. Our process allows for rapid validation of product design concepts and structural integrity.
- Free Sample Provision
- Lead Time: 10 business days
Precision Prototyping
We offer precision prototyping services that allow you to bring your concepts to life with exacting detail. Our advanced techniques ensure that prototypes are not only accurate but also provide a clear pathway to full-scale production.
- Lead Time: 7-14 business days
Quality Control
At Plantmetal, we are dedicated to fostering a culture of total company engagement, where every employee is empowered to enhance quality and boost productivity. This commitment, aligned with our continuous efforts to improve our quality management system, guarantees our ability to not only meet but exceed our customers' expectations.
Our ISO and IATF certifications confirm our status as a certified manufacturer of precision stampings, wireforms, metal components, and assemblies. We rigorously uphold these certifications to assure our clients of our unwavering commitment to delivering superior service and exceptional product quality.
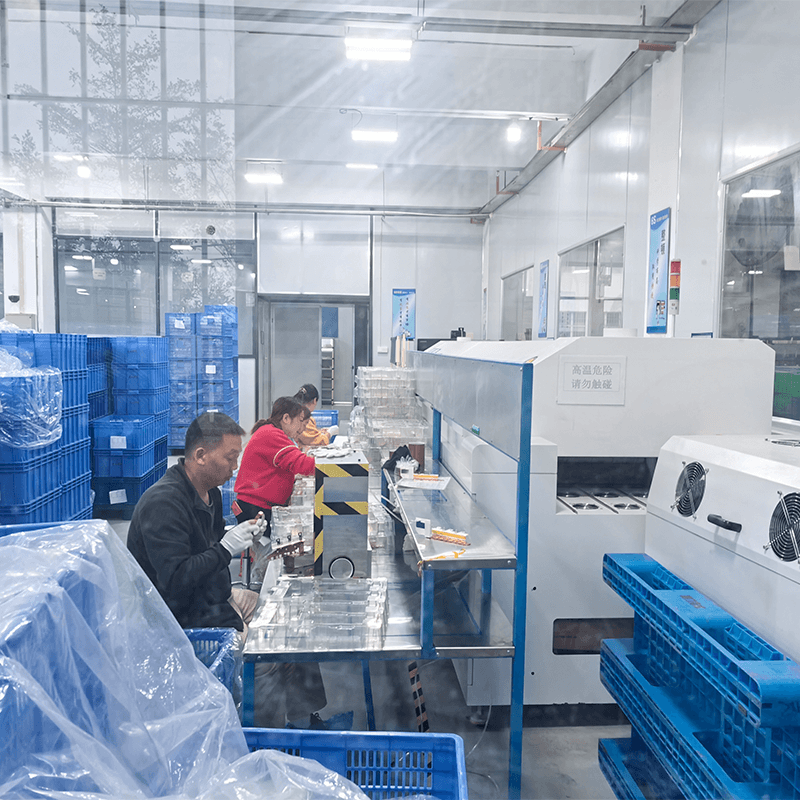
Quality Policy
Our commitment to excellence drives us to continually enhance our processes, ensuring the delivery of metal stamping components that meet the highest standards of quality and service. We rigorously adhere to industry standards and regulations to achieve this.
Every team member is dedicated to upholding the ISO 9001:2015 quality management system throughout all stages of production, from material receipt through to final delivery. We meticulously ensure that each product meets the specific requirements of our customers.
Quality Objectives
- Reduce Tool Setup Time: Achieve a 70% or greater reduction in tool setup time compared to industry averages in the stamping sector.
- Minimize Reject Rate: Maintain a reject rate of less than 1%, with a commitment to replacing any defective parts with high-quality replacements.
- Enhance On-Time Delivery: Improve on-time delivery performance to 98% or higher.
At our company, quality control is meticulously managed throughout every stage of production. We utilize advanced machinery and systems to meet our customers' specific requirements, and we work with reliable suppliers to ensure consistent quality and traceability of all materials.
Our ability to meet precise quality standards is attributed to our skilled quality technicians and production team. By employing tools such as PPAP (Production Part Approval Process) and SPC (Statistical Process Control), we effectively ensure that our commitments are consistently fulfilled.
Our quality department is equipped with comprehensive tools for rigorous inspections, including material incoming checks, first article inspections, in-process monitoring, and final quality assessments.