CNC Machining Service
- Focus On Custom CNC Machining Manufacturing
- One-demand services
- 10 days delivery after order
- 3 axis,4 axis & 5 axis CNC machining
Our CNC Machining Capabilities
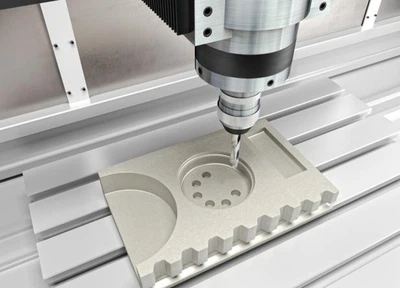
CNC Milling
For custom parts requiring exact tolerances and smooth, flat surfaces, our 3-axis and 5-axis CNC milling services are the ideal solution. We deliver machined components with precision tolerances as tight as 0.01mm, ensuring high-quality results for your most demanding applications.
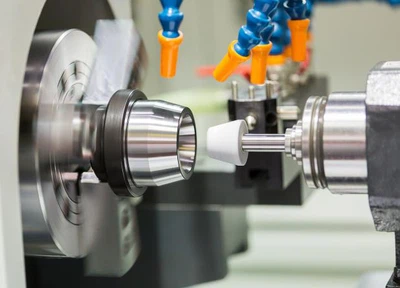
CNC Turning
CNC turning offers an efficient and cost-effective solution for manufacturing cylindrical components such as pins, shafts, and spacers, or any parts requiring rotational symmetry. Our precision lathes are designed to deliver high-quality results with exceptional accuracy and consistency.
Why Choose Plantmetal for CNC Machining
At Plantmetal, our CNC machining services are characterized by precision and efficiency. As a trusted partner for quality manufacturing, we offer:
- Advanced 5-Axis CNC Machines: Our state-of-the-art 5-axis machines enable us to produce complex components with fewer setups and enhanced accuracy.
- Versatile Part Production: We handle CNC machining for parts ranging from 0.2 inches to 8 inches in diameter and up to 20 inches in length.
- Cutting-Edge CAM Software: Our use of advanced CAM software optimizes tool paths and reduces manufacturing costs, ensuring efficient production.
- Automatic Tool Changers: Equipped with automatic tool changers, our CNC machines minimize setup times and boost productivity.
CNC Machined Parts Showcase
We specialize in machining rapid prototypes and low-volume production runs for clients across various sectors, including aerospace, automotive, defense, electronics, industrial automation, machinery, medical devices, oil & gas, and robotics.
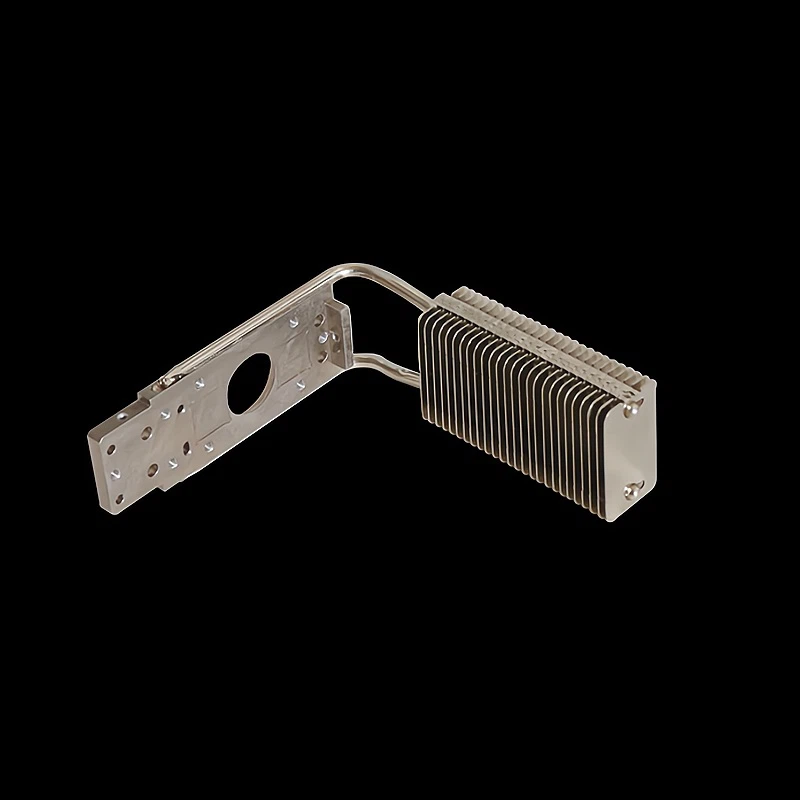
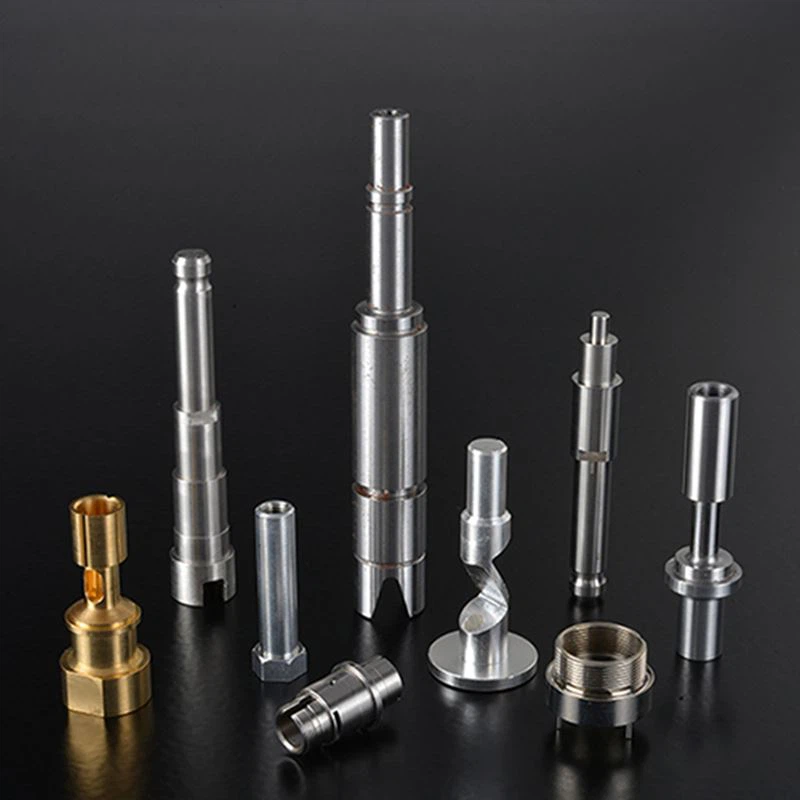
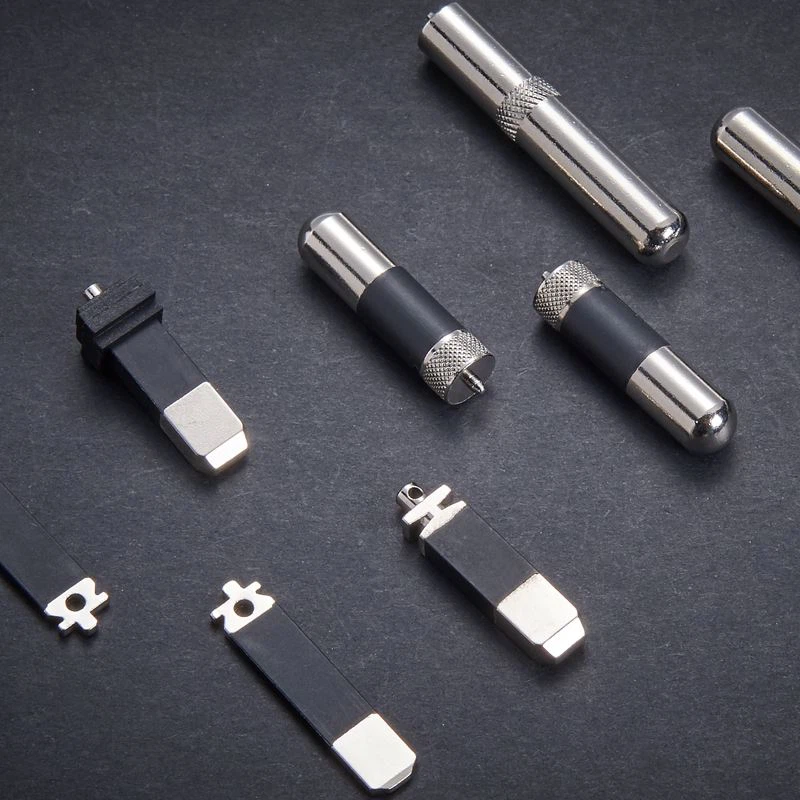
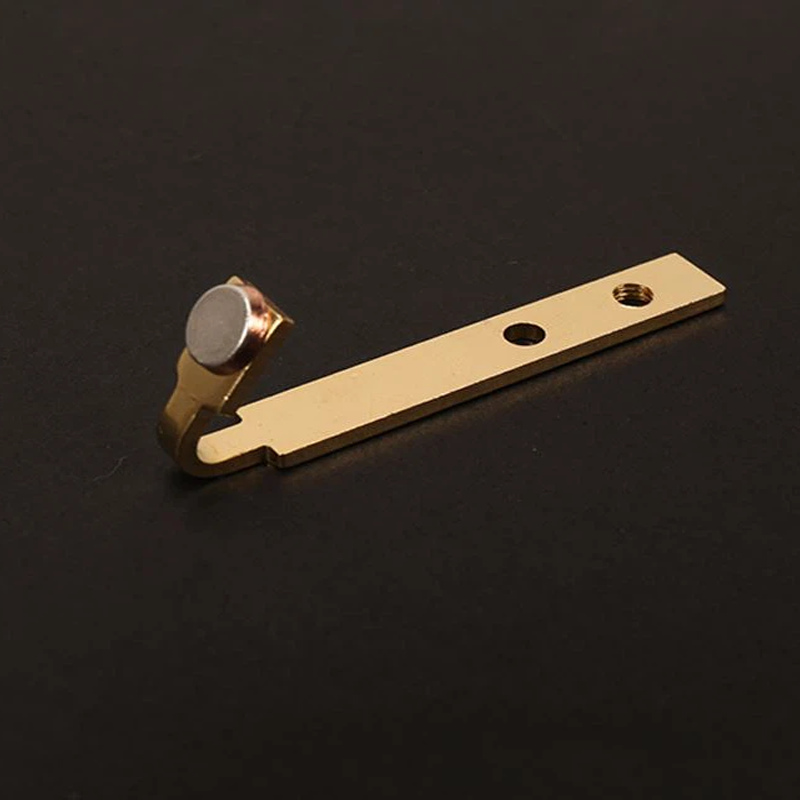
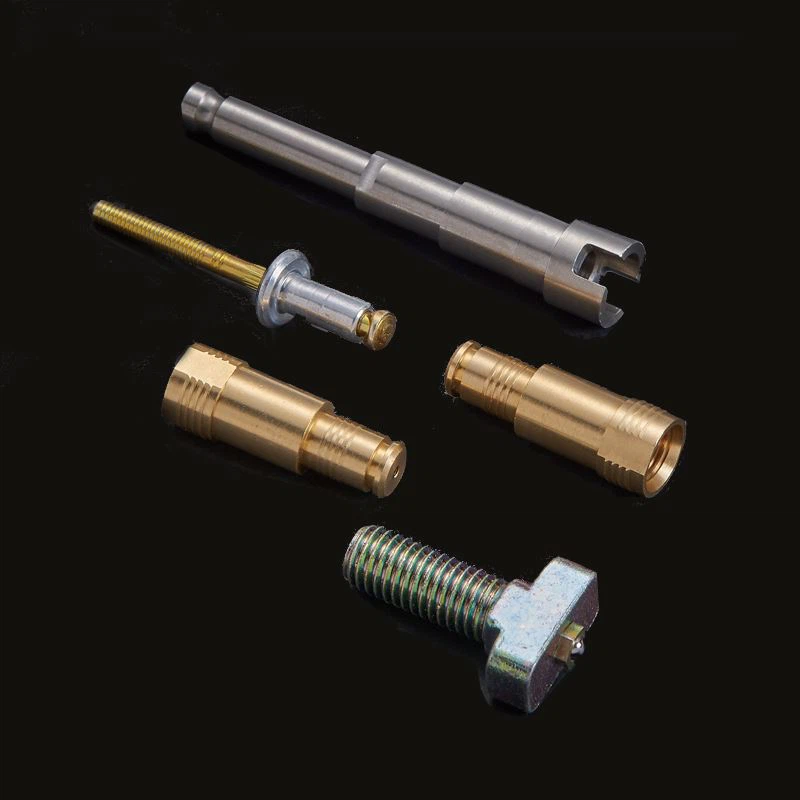
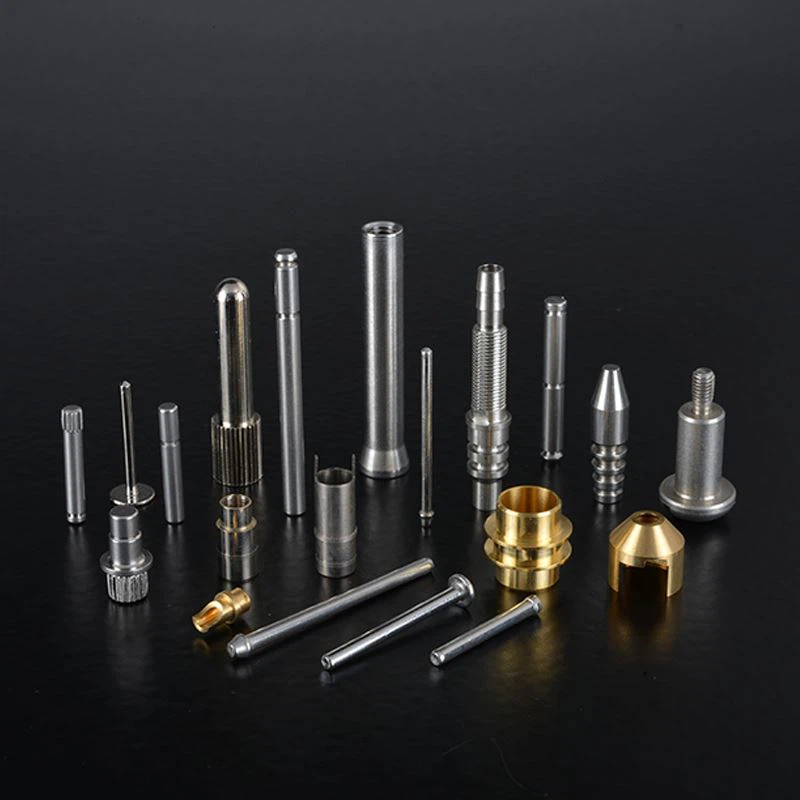
Material For Custom CNC Machining Parts
Copper
Copper is renowned for its excellent electrical and thermal conductivity, as well as its robust mechanical properties and favorable workability.
Types:
- C11000: Known for its high electrical conductivity.
- HPB59: A high-performance copper alloy with enhanced mechanical properties.
Aluminum
Aluminum is a lightweight, corrosion-resistant metal known for its high strength and excellent machinability.
Types:
- 1050, 1060: Pure aluminum with high corrosion resistance and good workability.
- 2024, 2A16, 2A02: High-strength alloys suitable for aerospace and structural applications.
- 3003, 3A21: General-purpose alloys with good formability and moderate strength.
- 4A01: Known for its good strength and excellent machinability.
Steel
Steel is a widely utilized metal primarily composed of iron alloyed with carbon and other elements to enhance its properties.
Types:
- 12L14: A free-machining steel known for its excellent machinability and good mechanical properties.
- 1215: A low-carbon steel with superior machinability, often used for high-volume manufacturing.
- SUM22: A medium-carbon steel offering a balance of strength and machinability, commonly used in structural applications.
- SUS303: An austenitic stainless steel with good machinability and resistance to oxidation, suitable for manufacturing parts requiring corrosion resistance.
Brass
Brass is an alloy of copper and zinc, characterized by its distinctive reddish-gold hue. It is widely used in applications requiring low friction and good machinability.
Types:
- C3601: Known for its excellent machinability and good corrosion resistance, often used in precision machining applications.
- C3602: Offers high strength and machinability, suitable for manufacturing components that need to withstand wear.
- C3603: Provides good mechanical properties and corrosion resistance, commonly used in plumbing fittings and electrical connectors.
- C3604: Features high ductility and excellent machinability, ideal for intricate, high-precision parts.
Plastic
Our CNC machining services accommodate a diverse array of plastic materials, from standard options to specialized varieties.
Types:
- ABS (Acrylonitrile Butadiene Styrene): Known for its impact resistance and toughness, making it ideal for a variety of industrial and consumer applications.
- PTFE (Polytetrafluoroethylene): Offers exceptional chemical resistance and low friction, suitable for applications requiring high durability and stability.
- PVC (Polyvinyl Chloride): Provides good mechanical properties and chemical resistance, commonly used in piping, fittings, and electrical insulation.
- PE (Polyethylene): Features excellent impact resistance and low friction, used in applications ranging from packaging to industrial components.
Custom Material Options
Based on customer specifications, including drawings, machining requirements, and performance needs, we offer a range of material choices tailored to your project.
Types:
- Zinc: Valued for its corrosion resistance and ease of machining, often used in die-casting and plating.
- Titanium: Renowned for its high strength-to-weight ratio and excellent corrosion resistance, suitable for aerospace, medical, and high-performance applications.
- Cast Iron: Known for its durability and wear resistance, commonly used in automotive and heavy machinery components.
- Nylon: Offers excellent mechanical properties, including high tensile strength and impact resistance, ideal for applications requiring toughness and wear resistance.
Finishing Options For CNC Machining
Different surface treatments are available according to each project.
Pictures | Name | Variety | Description |
![]() |
Plating Treatment | chrome plating, zinc plating, nickel plating, electroplating, electrophoresis, etc | Coating a layer of metal or alloy on the surface of the part, the corrosion resistance, wear resistance, and aesthetics of the part can be improved. |
![]() |
Oxidation Treatment | anodizing, chemical oxidation, etc. | Forming a layer of oxide film on the surface of the part, its corrosion resistance, wear resistance, and aesthetics can be improved. |
![]() |
Coating Treatment | painting, powder spraying, etc. | Spraying a special coating on the surface of the part, its anti-corrosion, wear resistance, and aesthetics can be improved. |
![]() |
Heat Treatment | quenching, tempering, normalizing, annealing, etc. | By heating the part to a specific temperature and then cooling it under suitable conditions, the material's physical properties can be improved, such as strength, toughness, and wear resistance. |
![]() |
Polishing Treatment | mechanical polishing, chemical polishing, etc. | Mechanical grinding or chemical treatment, the surface of the part can be made smooth and bright, which increases its aesthetics and tactile sensation. |
![]() |
Grinding Treatment | mechanical grinding, chemical grinding, etc. | Using a grinding process, the surface of the part can be made to meet the required smoothness and precision, increasing its precision and aesthetics. |
![]() |
Sandblasting Treatment | / | The part's surface can be uniformly and finely scratched using a high-pressure sandblasting process, increasing its aesthetics and anti-slip properties. |
![]() |
Chemical Treatment | acid washing, alkaline washing, etc. | Using a chemical reaction, the surface of the part can undergo a chemical change, improving its performance or aesthetics. |
FAQs About CNC Machine
Q: What factors influence the cost of CNC machined parts?
A: The cost of CNC machined parts varies and is influenced by several factors including the complexity of the part, material choice, machining time, tolerance requirements, and the order quantity. Each of these elements contributes to the overall pricing.
Q: Can CNC machined parts be customized?
A: Yes, CNC machined parts can be customized to meet specific requirements. We offers tailored solutions by modifying CAD models, adjusting toolpaths, and fine-tuning machining parameters to align with the customer's unique needs.
Q: What is the maximum size for CNC machined parts?
A: Plantmetal can produce CNC machined parts with diameters ranging from 0.2 inches to 8 inches and lengths up to 20 inches.
Q: What level of precision can be achieved with CNC machining, and how is this precision maintained?
A: CNC machining typically achieves high precision, often within a few thousandths of an inch (0.025 mm) or tighter, depending on the machine and part requirements. This precision is maintained through factors such as advanced machine technology, precise computer control, meticulous calibration and setup, and rigorous quality control measures.