What is Deep Drawing?
Deep drawing is a metal forming process used to shape sheet metal into complex, hollow shapes by applying mechanical force with a punch that draws the metal into a die. This process is ideal for creating seamless, intricate parts like cups, cylinders, and deep hollow enclosures. The method can handle a variety of metal materials and is used across multiple industries, including automotive, aerospace, medical, and consumer electronics.
In the deep drawing process, a flat metal sheet, or blank, is placed over a die and pressed into the desired shape using a punch. The metal flows into the die cavity to form the required geometry, often requiring multiple drawing operations (redrawing) to achieve deeper shapes without compromising the material's strength or structure.
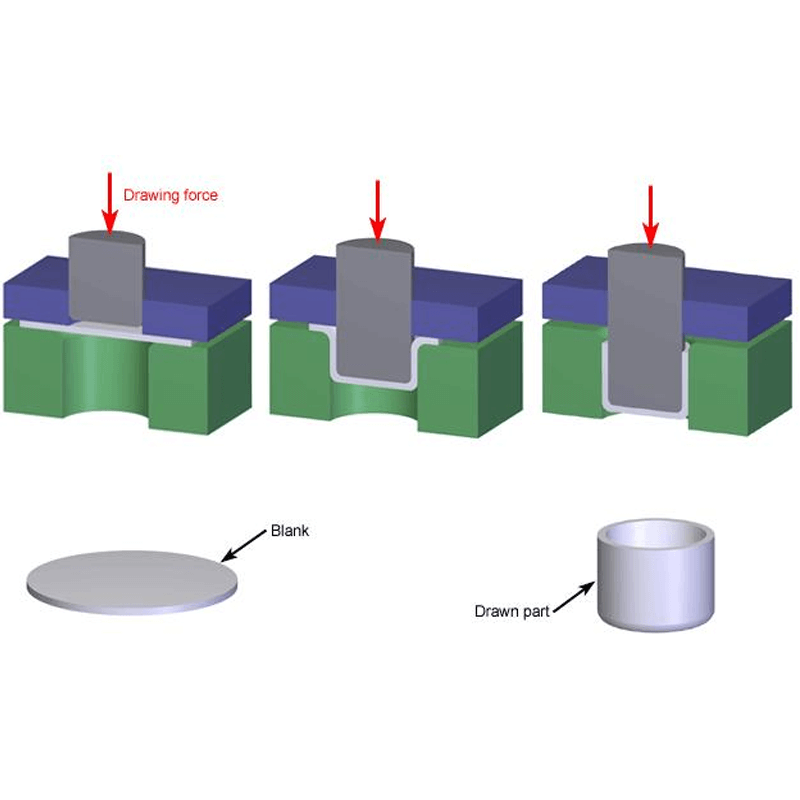
Deep Drawing Production Process
The deep drawing process involves several critical stages, each essential to ensuring the quality and precision of the final product:
1. Blank Preparation
The process begins with cutting the flat sheet metal into a specific shape known as a blank. The blank size must be calculated to ensure the appropriate amount of material is available for forming while minimizing waste.
2. Lubrication
Lubrication is applied to the blank and the die surface to reduce friction during forming, preventing excessive wear on tools and minimizing material defects.
3. First Drawing
The punch forces the blank into the die during the initial drawing stage, creating the basic shape. Multiple drawing operations might be needed depending on the part's depth and complexity.
4. Redrawing
For deeper parts, redrawing is required. After the initial drawing, the part is transferred to another die where the drawing operation continues to achieve the desired depth. This step ensures uniform wall thickness and avoids tearing or wrinkling of the material.
5. Trimming and Finishing
After the drawing process, excess material around the edges of the part is trimmed away to give it its final shape. Depending on the application, finishing processes such as deburring, polishing, or coating may also be applied.
6. Inspection and Quality Control
Each part undergoes rigorous inspection and quality control checks to ensure it meets exact specifications. Parameters such as thickness, surface finish, and dimensional accuracy are verified before shipment.
Materials Used in Deep Drawing
The choice of material is crucial for successful deep drawing. Each metal behaves differently under stress, and selecting the right one for your application ensures optimal performance and longevity of the finished part. Below is a table summarizing the materials commonly used in the deep drawing process:
Material | Key Properties | Applications |
Aluminum | Lightweight, corrosion-resistant, easy to form, high strength-to-weight ratio | Automotive parts, electronics enclosures, cans |
Stainless Steel | High corrosion resistance, strong at high temperatures, excellent durability | Kitchenware, medical equipment, aerospace components |
Brass | Good corrosion resistance, excellent electrical conductivity, easy to form | Electrical connectors, plumbing fittings, jewelry |
Copper | Excellent electrical and thermal conductivity, corrosion-resistant, easy to form | Electrical parts, heat exchangers, plumbing tubes |
Titanium | Lightweight, high strength, corrosion-resistant, biocompatible, strong in extreme environments | Aerospace parts, medical implants, marine equipment |
Cold Rolled Steel | Economical, high strength, easily machinable | Automotive panels, appliance parts, industrial tools |
Why Choose Plantmetal for Your Deep Drawing Needs?
When selecting a partner for your deep drawing projects, precision, reliability, and customization are paramount. Here are six compelling reasons why our factory stands out as the ideal choice:
High-Quality Materials
We work with a wide range of metals, ensuring we can meet diverse industry demands. Our materials range from aluminum and stainless steel to copper, brass, and titanium, all sourced from trusted suppliers to guarantee top-tier performance and durability.
Advanced Equipment
Our factory is equipped with state-of-the-art deep drawing machinery capable of producing intricate parts with tight tolerances. This ensures that we can handle both high-volume production and smaller custom orders with equal precision.
OEM Services
As an OEM provider, we offer end-to-end services, from initial design consultation and prototyping to full-scale production and assembly. Our deep drawing expertise allows us to develop tailor-made solutions that meet your exact specifications, helping you bring your products to market faster and more efficiently.
Experienced Engineering Team
Our engineers bring years of experience in deep drawing and metal forming to each project. They collaborate closely with clients, providing valuable insights into material selection, process optimization, and design improvements, ensuring that every part is engineered for success.
Competitive Pricing
With a lean manufacturing approach and a focus on reducing waste, we offer competitive pricing without compromising quality. Our production process is optimized to minimize material usage and maximize efficiency, translating to cost savings for our clients.
Commitment to Quality and Precision
We are ISO9001 certified, adhering to the highest quality management standards. Each step of our deep drawing process is subject to rigorous quality control checks, ensuring that every part meets or exceeds your expectations for precision, durability, and finish.
Additional Considerations in Deep Drawing
Tooling Design
The tooling design is a critical factor in ensuring the success of any deep drawing project. Proper die and punch design minimizes the risk of defects such as wrinkling, tearing, or thinning of the material. Our engineering team uses advanced CAD software and simulations to design custom tooling that optimizes material flow and reduces wear on the tools, extending their lifespan and improving the overall quality of the final parts.
Material Thickness and Draw Ratio
When planning a deep drawing operation, the draw ratio (the ratio of the blank diameter to the punch diameter) is an essential consideration. A higher draw ratio typically means the material undergoes more deformation, which requires careful control to avoid defects. Material thickness also plays a role in determining the feasibility of a deep drawing project. Thicker materials may require higher forces and more advanced equipment to achieve the desired depth without wrinkling or tearing.
Surface Finishing
Deep-drawn parts often require additional finishing processes to meet aesthetic or functional requirements. Depending on the application, surface treatments such as electroplating, anodizing, powder coating, or polishing may be applied to improve corrosion resistance, enhance appearance, or provide electrical insulation. We offer a range of finishing options to meet the specific needs of our clients.
Reducing Costs through Process Optimization
One of the main challenges in deep drawing is maintaining high quality while keeping costs in check. By optimizing the blank size, tooling design, and drawing stages, we help our clients reduce material waste and minimize production time. This ensures that projects stay within budget without compromising the final product's integrity or performance.
Precision Deep Drawing Solutions for Industry Applications
Deep drawing is a versatile and highly effective metal forming technique capable of producing intricate, high-quality parts for a variety of industries. Our factory combines the latest technology, expert engineering, and comprehensive OEM services to deliver deep-drawn components that meet the strictest industry standards. With our commitment to quality, precision, and customer satisfaction, we are your ideal partner for all your deep drawing needs. Contact us today to learn more about how we can help with your next project!
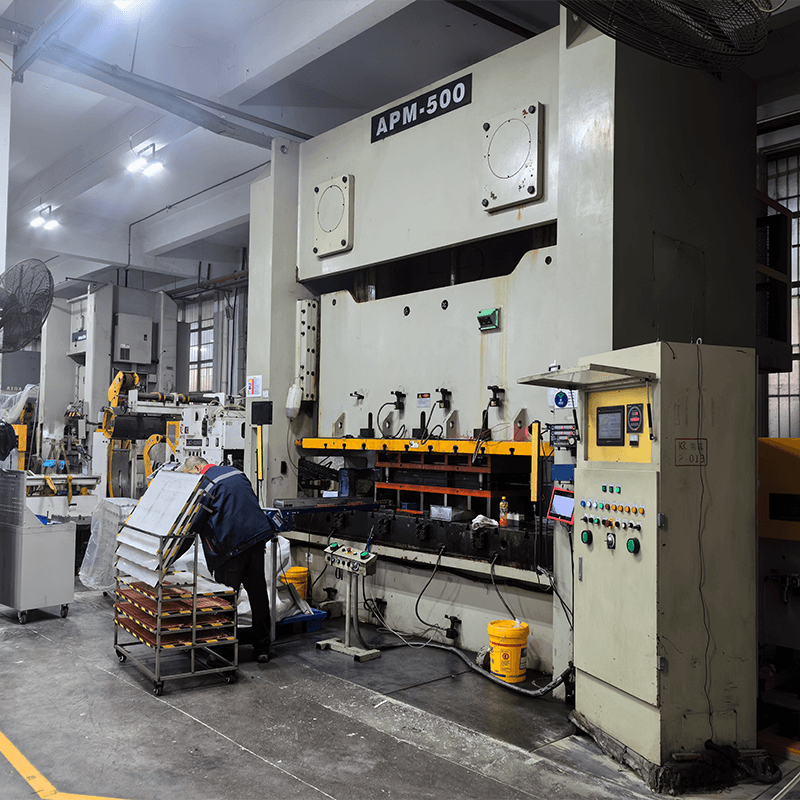