Capabilities in Electrical Contact Rivet Assemblies
Plantmetal offers tailored welding and riveting solutions to meet the unique requirements of its customers, leveraging state-of-the-art automation equipment.
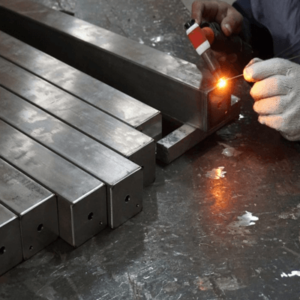
Welding
Welding plays a crucial role in the fabrication of contact assemblies. At Plantmetal, we achieve seamless connections between electrical contacts and other electronic components through a combination of precision mold production and automated welding techniques.
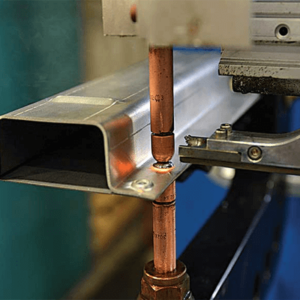
Riveting
Riveting involves applying force and pressure to securely join contacts with other components, resulting in a robust, unified structure. Plantmetal’s production line features cutting-edge automated riveting equipment, ensuring consistent and reliable connections.
Tailored Manufacturing Solutions for Your Project
Electric contacts, crafted from robust metal materials, are designed to endure high-frequency, high-voltage, and high-current conditions. Electric contact assemblies, which combine these contacts with additional electronic components, are essential in numerous applications, including automotive systems, electrical appliances, and various electronic devices. We offer customized solutions, designing and manufacturing electric contacts and assemblies to meet the unique specifications of your project.
Available Types of Electrical Contacts
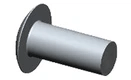
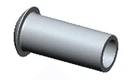
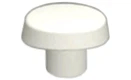
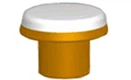
Portfolio of Electrical Contact Assemblies
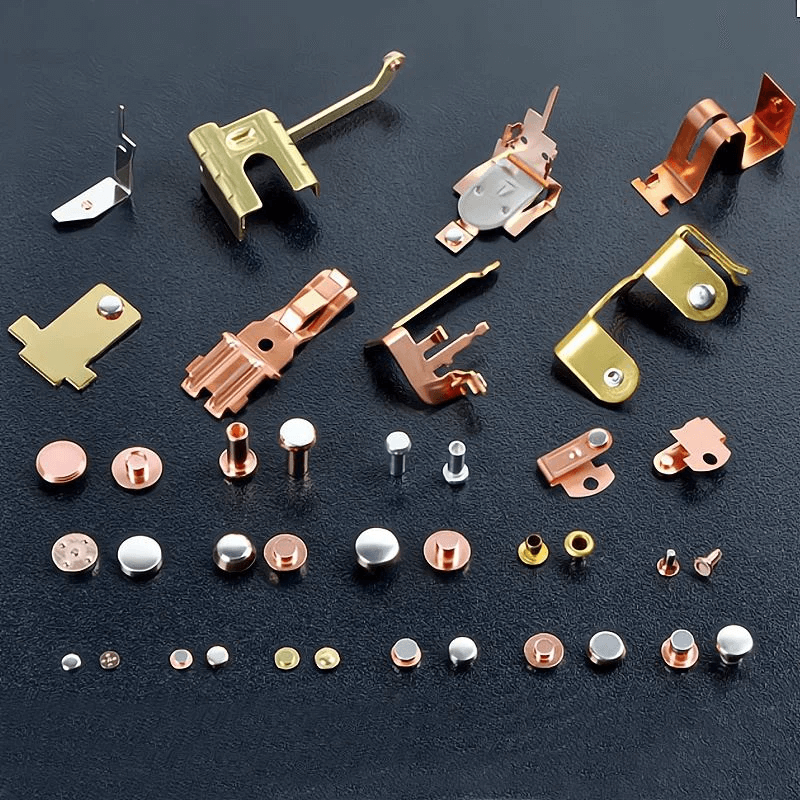
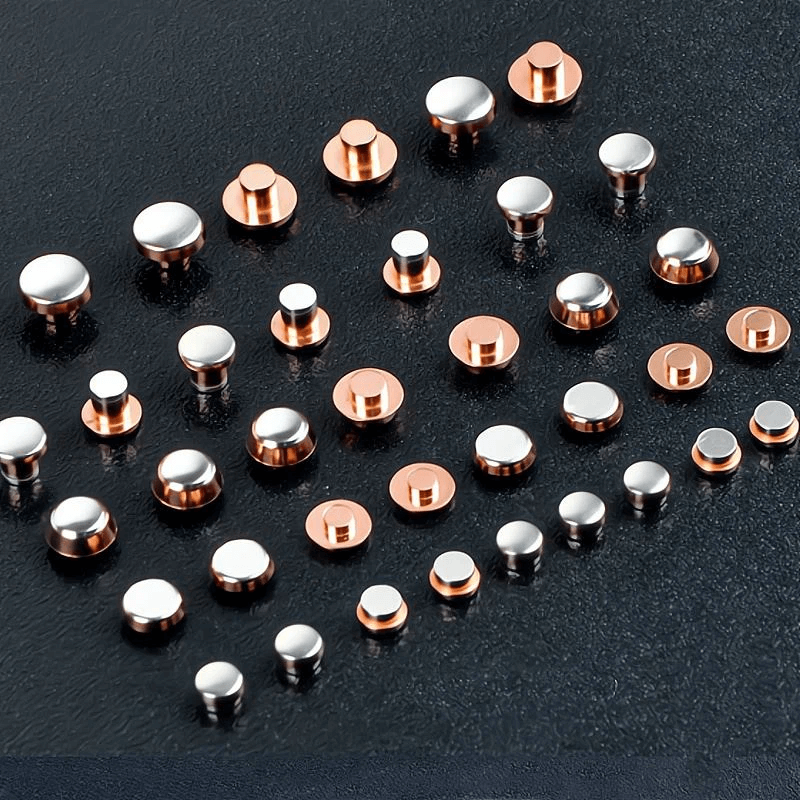
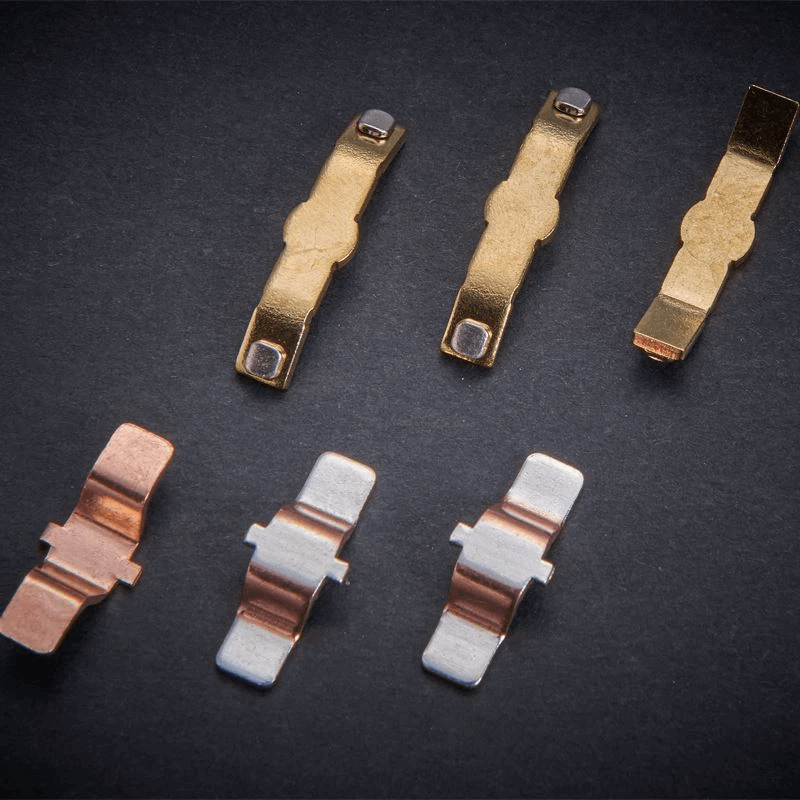
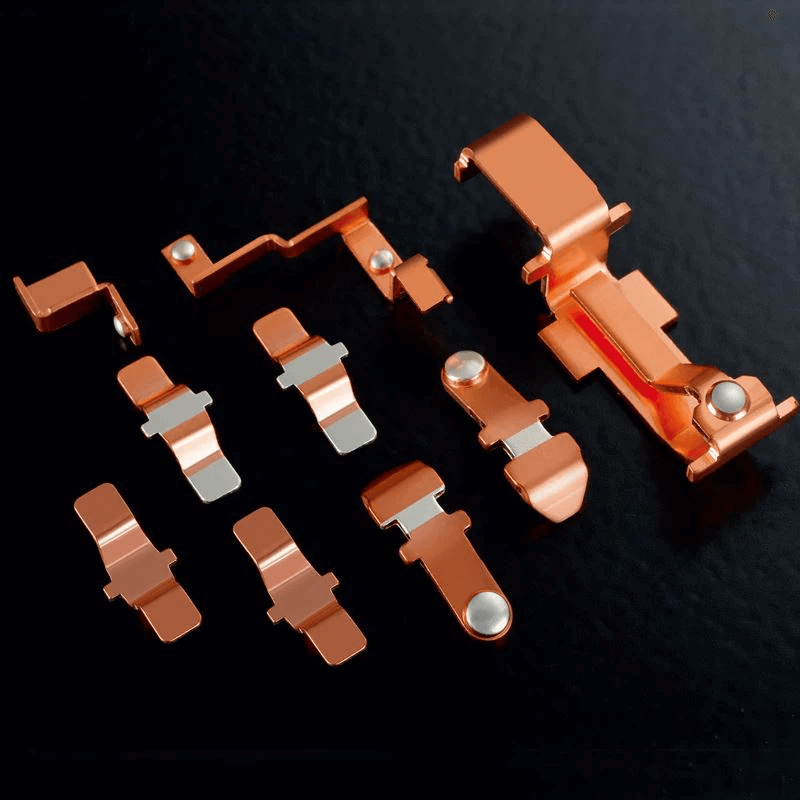
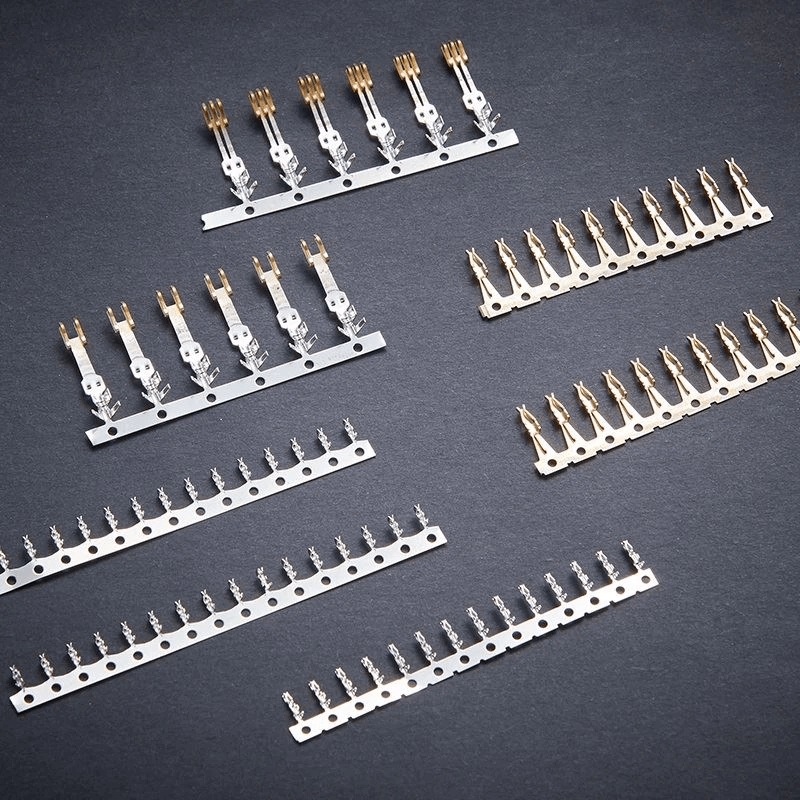
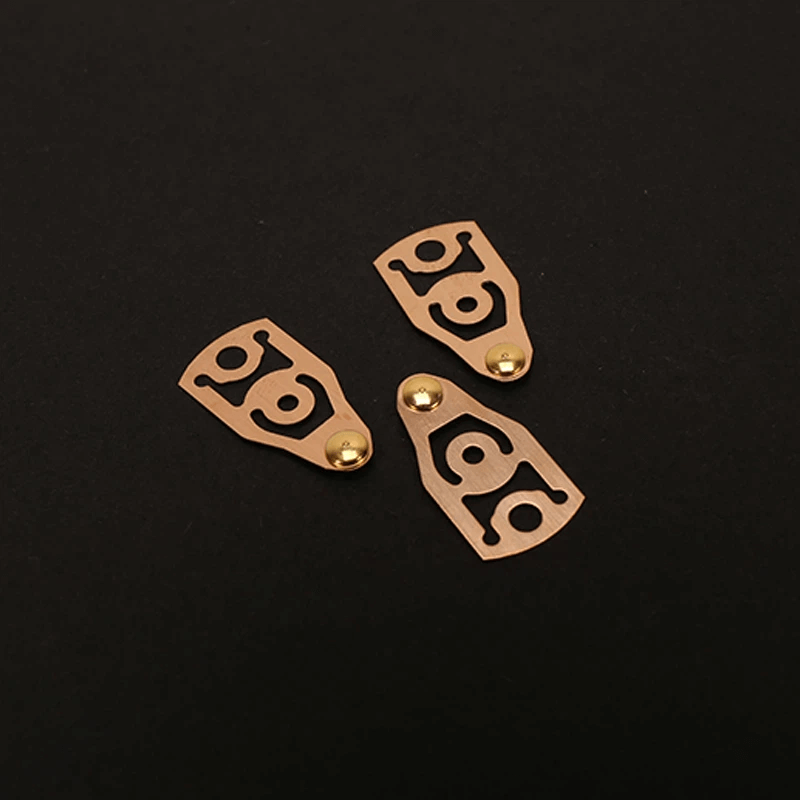
How It Works
1. Receive a Quote
Upload your CAD files, and we will provide a quote within 24 hours. If CAD drawings are not available, please send us a sample of the product for evaluation.
2. Confirm Specifications
Our engineering team will review your requirements and finalize the manufacturing process and tolerance details in a collaborative meeting.
3. Commence Production
Production will begin promptly once the order is confirmed. We will keep you informed with real-time updates on the progress.
4. Delivery of Custom Parts
Your custom parts will be securely packaged and delivered according to the specified shipping and handling instructions.
Metal Strip Contact Assemblies
For optimal performance in electrical contact assemblies, high-conductivity metal materials are essential. Typically, these include brass stamping components and various other metals, which are crucial for effective connectivity. Common materials used in these assemblies are:
- Copper
- Brass
- Copper Alloy
- Red Copper
- Aluminum Alloy
- Phosphor Bronze
- Beryllium Bronze
- Custom Specifications
These materials are often utilized in components such as springs, contact fingers, and metal clips, ensuring reliable electrical connectivity and performance.
Why Choose Plantmetal?
Flexible Order Handling
Plantmetal accommodates both small and large orders. For smaller batch requests, our engineering team assesses the most effective production approach to deliver competitive pricing while maintaining top-tier quality.
Efficient Large-Scale Production
Leveraging state-of-the-art technologies such as in-mold welding and automated riveting, we achieve high-efficiency production with a capacity of up to 2,000 units per hour, significantly reducing per-unit costs.
Precision and Excellence
With over 20 years of expertise in contact and contact assembly technologies, we ensure precise positioning and deliver products of the highest quality.
Comprehensive Support and Customization
Our commitment extends beyond production. We offer comprehensive support throughout the project lifecycle, from initial design consultation to final delivery, ensuring that every component meets your specific requirements and performance standards.
Applications of Our Contact Assemblies
1. Power Systems
Our contact assemblies are integral to high-performance power systems, providing reliable connections in applications that require robust electrical conductivity and durability. These assemblies are used in power distribution systems, energy management solutions, and high-current power connections, ensuring stable and efficient operation across various industrial and commercial power infrastructures.
2. Electronic Instrumentation
In electronic instrumentation, our contact assemblies facilitate precise and stable connections within sophisticated measurement and control devices. They are essential for ensuring accurate data transmission and reliable performance in scientific instruments, diagnostic equipment, and advanced electronic sensors, where precision and reliability are critical.
3. Socket & Plug Systems
Our contact assemblies play a crucial role in socket and plug systems, offering reliable electrical connections in a wide range of applications, from consumer electronics to industrial machinery. These assemblies ensure secure and efficient power transmission, enhancing the performance and safety of electrical connections in both residential and commercial environments.
4. Switches
Our assemblies are designed for use in various types of switches, including toggle switches, push-button switches, and rotary switches. They provide consistent and dependable electrical contacts, contributing to the reliable operation of control mechanisms in diverse applications such as automotive controls, household appliances, and industrial equipment.
FAQs
Q: What is an electrical contact assembly?
A: Electrical contact assemblies refer to integrated components such as connectors, switches, relays, and circuit breakers, where multiple contacts are assembled to establish effective electrical connections. These assemblies are typically manufactured using methods like soldering, welding, or crimping to securely join the contacts and connect them to the relevant wiring or circuitry.
Q: Do you offer customized solutions for electrical contact assemblies?
A: Yes, we offer bespoke solutions for electrical contact assemblies. Our skilled engineering team collaborates with clients to develop custom assemblies tailored to their specific requirements, ensuring optimal performance and functionality for your unique application.
Q: What is the process for manufacturing metal parts?
A: The manufacturing of metal parts involves a comprehensive process that includes design development, material selection, fabrication, machining, and finishing. The process starts with creating or receiving design specifications, followed by precise fabrication and machining to produce the final metal components.
Q: How can I guarantee the reliability and longevity of electrical contacts?
A: Ensuring the reliability and durability of electrical contacts involves several critical factors: selecting appropriate materials, designing to exact specifications, maintaining surface cleanliness, applying suitable lubricants, and considering environmental conditions. Each of these aspects plays a crucial role in achieving long-lasting and dependable electrical performance.