What Is Metal Injection Molding (MIM)
Metal Injection Molding (MIM) is a sophisticated metalworking technique that enables the production of intricate and highly customized metal components. This process is ideal for manufacturing small, complex metal parts that are not readily available off the shelf, typically weighing under 100 grams.
MIM offers significantly greater design flexibility compared to traditional metal fabrication methods like die casting. By utilizing a combination of metal powders and plastic binders, manufacturers can achieve highly complex geometries that would be difficult or impossible to produce using other methods. This process is particularly valuable for creating bespoke metal components with precise specifications.
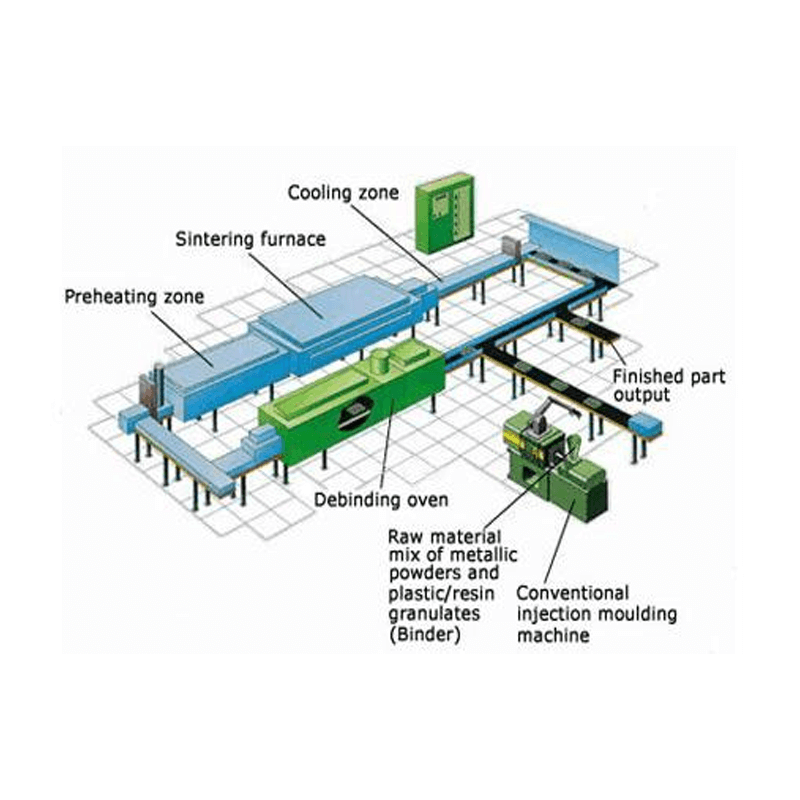
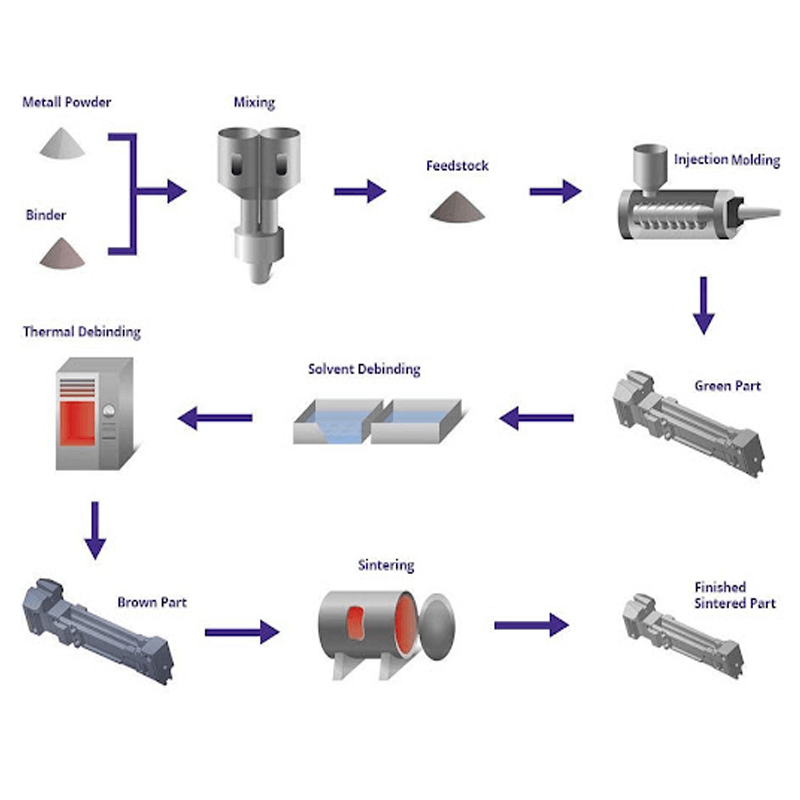
Metal Injection Molding Process
1.Feedstock Preparation: The Metal Injection Molding (MIM) process begins by finely grinding metal powders and blending them with a binding material to form a homogeneous mixture known as "feedstock." Simultaneously, a mold is designed to shape the final product.
2. Injection Molding: The prepared feedstock is injected into the mold, where it takes the desired shape and solidifies. This step is crucial in forming the initial structure of the component.
3. Debinding: After molding, the component undergoes a debinding process to remove the binder material. The debinding method varies depending on the specific binder used. This step typically involves multiple cycles to ensure thorough removal of the binder, leaving the part semi-porous and ready for the subsequent sintering stage.
4. Sintering: The final step is sintering, where the debound part is heated to a high temperature, causing the metal particles to bond together. This process finalizes the component’s wall thickness, geometry, material composition, and physical properties. Sintering ensures that the parts achieve the necessary strength and durability, allowing for the efficient production of high volumes of precise components.
The Advantages of Metal Injection Molding (MIM) for Custom Metal Fabrication
Metal Injection Molding (MIM) offers several significant advantages over traditional metal fabrication techniques.
First and foremost, MIM provides unparalleled flexibility in creating custom metal components that are often unavailable through conventional manufacturing processes. Whether designing a small, unique fastener, a specialized spring, or high-strength bolts, MIM enables product designers to realize their visions without being constrained by the limitations of standard market offerings.
Moreover, MIM excels in producing parts with intricate geometries and complex metal compositions. This process allows designers to confidently craft detailed and sophisticated shapes while selecting from a broad range of metals, including iron, cobalt alloys, and stainless steel, to meet specific performance requirements.
Additionally, MIM offers the capability to mold or imprint words and numbers directly into the component, a feature that is typically challenging or impossible to achieve with conventional machining methods. The process also allows for the creation of thin-walled parts that are stronger and more durable than those produced by traditional means.
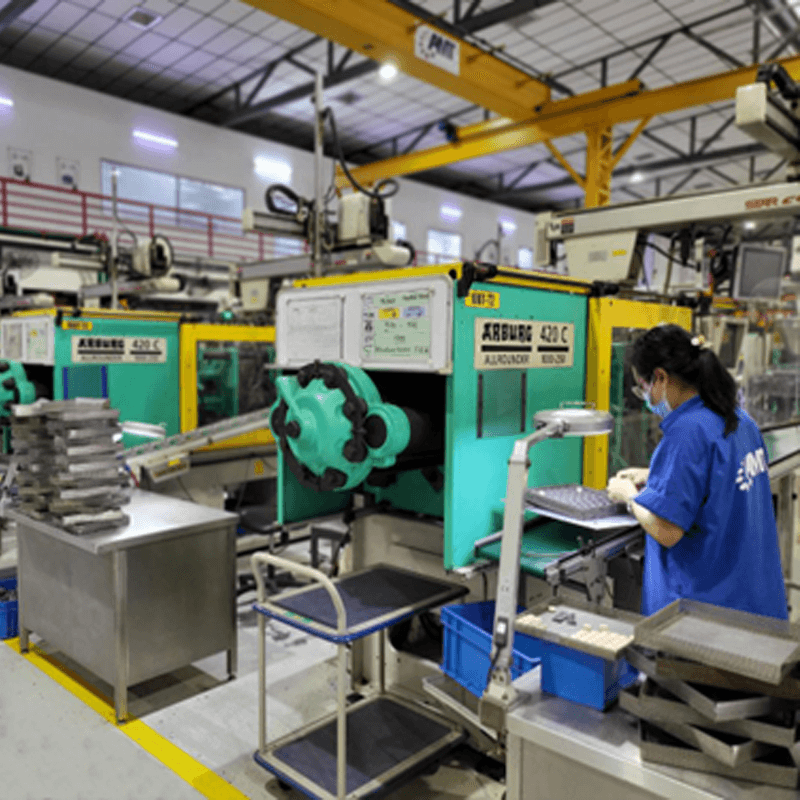
Why Choose Us for Your Metal Injection Molding Needs
- High Reproducibility, Even in Large Volumes: Our MIM process ensures consistent quality and precision across even the largest production runs.
- Cost-Effective, Ready-to-Install Components: We deliver fully finished parts at competitive unit costs, making them ready for immediate use.
- Maximized Material Utilization: With a material yield approaching 100%, we minimize waste and optimize efficiency.
- Comprehensive Finishing Capabilities: We offer components at any stage of finishing, tailored to your specific needs.
- Environmentally Responsible Manufacturing: Our process emphasizes material and energy efficiency, contributing to environmental sustainability.
- Commitment to Recyclability: We prioritize the recyclability of our materials, further enhancing the eco-friendliness of our manufacturing processes.
Applications of Metal Injection Molding (MIM)
Medical Technology:
Metal injection molding excels in the production of high-precision instruments and components for diagnostic and therapeutic devices. From intricate parts for medical devices and spreaders to specialized components for surgical forceps and braces, MIM delivers unparalleled precision and reliability. Partner with us to innovate and advance medical technology with cutting-edge solutions.
Consumer Goods:
In the consumer sector, where quality, innovation, and sustainability are key, MIM stands out as a superior manufacturing process. Whether producing parts for luxury watches, smartwatches, razors, nail files, handbags, binoculars, or digital cameras, MIM offers limitless possibilities, enhancing product quality while supporting sustainable production practices.
Aerospace:
Our MIM components have made history as the first safety-critical parts used in aviation. Engineered for aircraft engines, these components offer exceptional heat resistance and reduced weight, contributing to improved performance. The high reproducibility of MIM parts also ensures cost-effective production, making them ideal for the aerospace industry.
Automotive:
With extensive experience in the automotive industry, we supply custom MIM components that enhance safety and comfort in electric vehicles. From connector housings and copper components to shunts, shielding housings, and gear wheels, our MIM process produces wear-resistant and heat-resistant parts that meet the rigorous demands of modern mobility solutions.
FAQs About Metal Injection Molding
Q: What is metal injection molding used for?
A: Metal injection molding (MIM) is employed to manufacture intricate and high-precision metal parts. It is widely used across various industries, including medical devices, firearms, automotive, electronics, aerospace, industrial equipment, consumer goods, sporting goods, fire protection systems, and military and defense applications.
Q: Are metal injection molded parts strong?
A: Yes, metal injection molded components are known for their strength and durability. The strength of MIM parts is influenced by factors such as the type of metal alloy used, the size and distribution of metal powders, the sintering process, and the overall design of the component.
Q: Is metal injection molding cost-effective?
A: Although MIM requires specialized and often expensive equipment, it can be a cost-effective solution for producing complex, high-precision metal parts, especially in large production volumes where the per-unit cost decreases.
Q: How long does the metal injection molding process take?
A: The timeline for metal injection molding can vary widely based on the complexity of the part, the production volume, the materials used, and the specific MIM process applied. Typically, for standard high-volume production runs with relatively simple designs, the process—from tooling setup to final part production—can range from a few weeks to several months.
Q: What is the best metal for injection molding?
A: The ideal metal for injection molding depends on the specific requirements of the application. However, stainless steels like 17-4 PH and 316L are commonly favored in MIM due to their excellent combination of corrosion resistance, strength, and durability.