What Is Metal Stamping Dies
In metal stamping, a male punch exerts force on a sheet of metal, pressing it into a female die with a concave shape. This pressure shapes the metal to match the die’s contour without the use of heat. Depending on the design, the die can either form, cut, or perform both operations simultaneously.
Stamping dies come in various sizes and configurations, tailored to projects ranging from microelectronics to aerospace components. There are several specialized types of dies used in different stamping processes:
- Progressive Dies: These are employed in progressive stamping, where the metal strip undergoes a series of sequential cutting and bending operations while still connected to the strip. Progressive dies are used in multi-station stamping processes.
- Transfer Dies: Similar to progressive dies, transfer dies are used for sequential operations in high-volume manufacturing. Unlike progressive stamping, transfer stamping does not involve a continuous metal strip. Transfer dies are typically used for larger or deep-drawn components, which are moved between different stations.
- Line Dies: Designed for tandem-line stamping, line dies are ideal for large components and projects that cannot be efficiently produced with a single stamping press.
- Compound Dies: These dies perform both cutting and shaping operations in a single press stroke. They are efficient for processes that require simultaneous cutting and forming.
Choosing the appropriate stamping die depends on the specific manufacturing needs and the geometry of your component. Our experts can assist in selecting the most effective die for your project to ensure optimal results.
Cutting Operations for Stamping Dies
Stamping dies perform various forming and cutting operations on metal blanks. Among the diverse range of stamping operations, the following cutting methods are commonly utilized:
- Trimming: Trimming involves removing excess metal along the edges of a component to achieve a clean and precise finish. This operation ensures that the final product meets the required specifications.
- Blanking: Blanking cuts out a complete or partially complete component from a sheet of metal. This method is used to prepare the component for further processing or final finishing.
- Piercing: Piercing creates a hole, typically round or rectangular, at a specified location in the metal component. This operation is essential for components requiring precise hole placements.
- Shearing: Shearing involves cutting the metal workpiece along a straight line. This method is used to create straight-edged parts or trim excess material.
- Lancing: Lancing involves creating slits in a metal strip without fully severing it. This technique is often used to form part carriers in progressive stamping operations.
- Notching: Notching produces a series of inset notches along the perimeter of a metal strip. This operation is commonly used in progressive stamping to create specific patterns or features.
Each cutting operation plays a crucial role in achieving the desired shape and functionality of the stamped metal parts, depending on the specific requirements of the project.
The Process Of Tool Manufacturing
The development and manufacturing capabilities of molds are essential, as the quality and precision of the molds directly impact the overall quality and accuracy of the finished products.
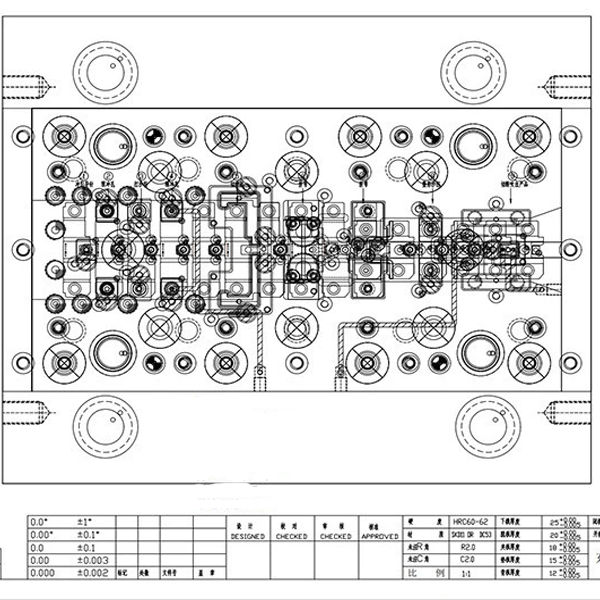
Step 1: Requirements Analysis (DFM)
In the initial stage of mold manufacturing, a thorough requirements analysis is essential. The Design for Manufacturability (DFM) process plays a crucial role in ensuring that the mold design aligns with manufacturing capabilities to minimize potential production challenges. Key considerations during this phase include bending radii, grooves, hole placements, material specifications, tolerances, wall thickness, and overall dimensions. This step is pivotal, as the effectiveness of the design significantly influences both the mold's manufacturing process and the quality of the final product.
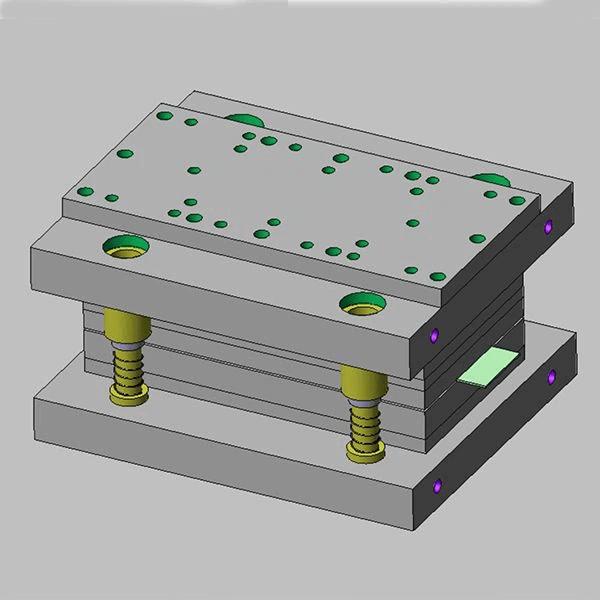
Step 2: Tooling Design
The tooling design phase focuses on developing a comprehensive 3D model of the mold, incorporating all essential components and features. This includes:
a. Stamping Process Parameters: Specifying factors such as pressure, speed, and frequency.
b. Mold Structure: Designing elements such as the mold base, upper and lower plates, guide columns, and springs.
c. Punch Specifications: Determining the positioning, quantity, size, and shape of the punches.
The placement of the punches is a critical aspect of mold design, as it directly influences the shape, dimensional precision of the stamped parts, production costs, and the mold’s longevity.
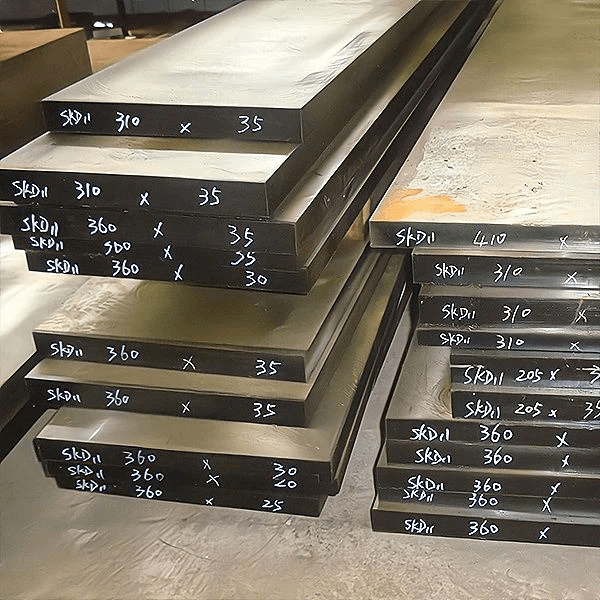
Step 3: Material Selection
Choosing the appropriate mold material is essential and depends on factors such as the type of part being produced, the precision required, and the anticipated production volume. Common materials include SKD11, D2, and CR12. The selected material must endure the stresses encountered during manufacturing while ensuring the production of parts with the necessary quality and consistency.
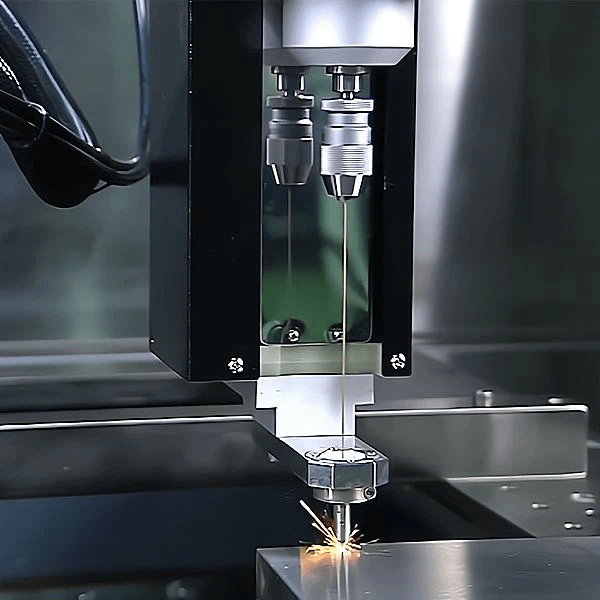
Step 4: Tool Machining and Heat Treatment
After selecting the mold material, it undergoes initial shaping through processes such as milling, turning, and drilling. For complex molds or high-precision inserts, Wire Electrical Discharge Machining (WEDM) is crucial to achieve the required intricacy and wear resistance.
Following machining, both the upper and lower mold components are subjected to heat treatment. This process enhances the material's strength and durability by altering its microstructure, thereby improving its mechanical properties.
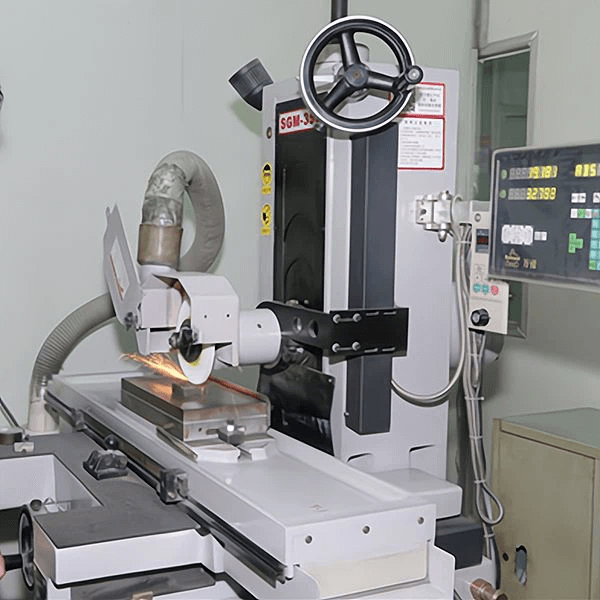
Step 5: Tool Finishing
To achieve the necessary surface finish and dimensional precision, the mold undergoes a meticulous finishing process. This stage may involve techniques such as grinding and polishing, tailored to meet the specific requirements of the final part. Finishing ensures that the mold delivers the desired level of accuracy and surface quality essential for high-precision components.
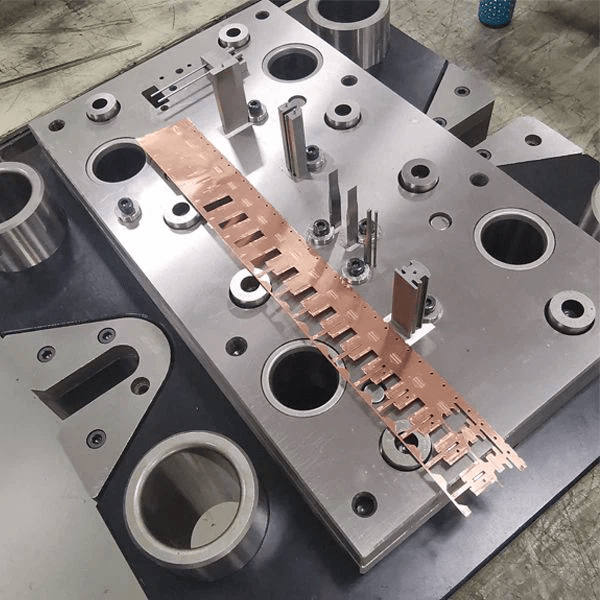
Step 6: Assembly and Testing
The final phase in the mold manufacturing process involves the assembly and rigorous testing of the mold. During this step, all mold components are assembled into their final configuration. The assembled mold undergoes a series of tests to verify that it meets all design specifications and produces parts with the required quality. This testing process includes producing sample parts, inspecting the mold for any defects, and making any necessary adjustments to ensure optimal performance and precision.
Advantages of Plantmetal For Your Metal Parts
Certifications
Our company is certified with IATF16949 and ISO13485, ensuring adherence to the highest industry standards for quality and precision.
Rapid Delivery
We offer expedited delivery services for all metal parts, ensuring prompt fulfillment of your orders.
Comprehensive After-Sales Support
Our overseas facilities provide local production capabilities, enhancing support and service for international markets.
Custom Solutions
We specialize in delivering tailored solutions to meet specific project requirements, leveraging our extensive expertise and advanced technology.
Tooling plays a pivotal role in the metal stamping process, with its design and fabrication being crucial to the success of any stamping project. At Plantmetal, we are dedicated to delivering optimal solutions tailored to your specific needs. Whether you require a straightforward stamping die or a sophisticated multi-stage tool, our expertise ensures that we can fulfill your unique tooling requirements with precision and excellence.